Kuhn RW 10 Series
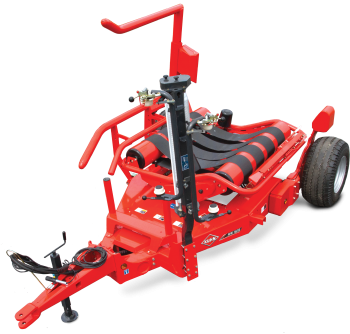
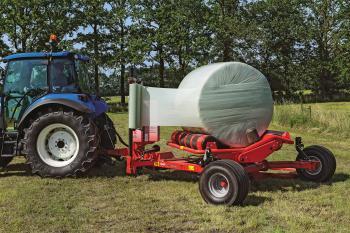
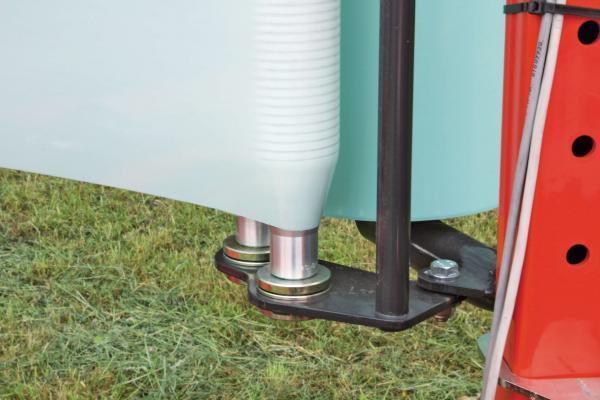
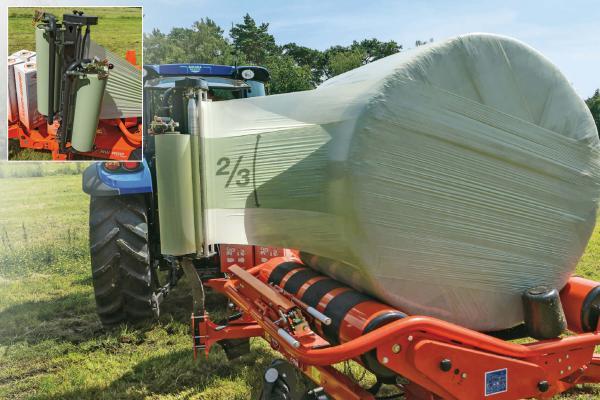
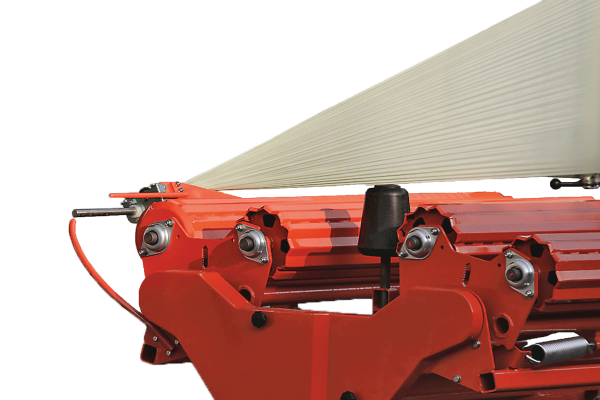
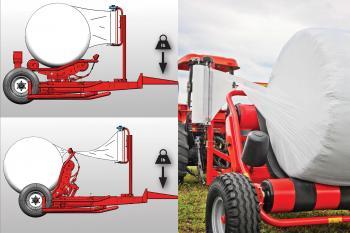
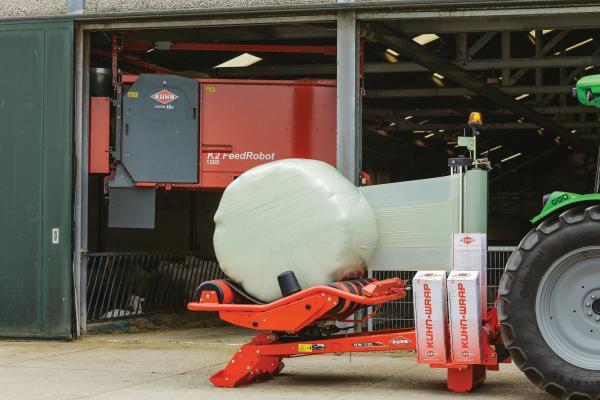
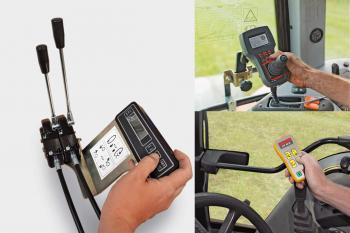
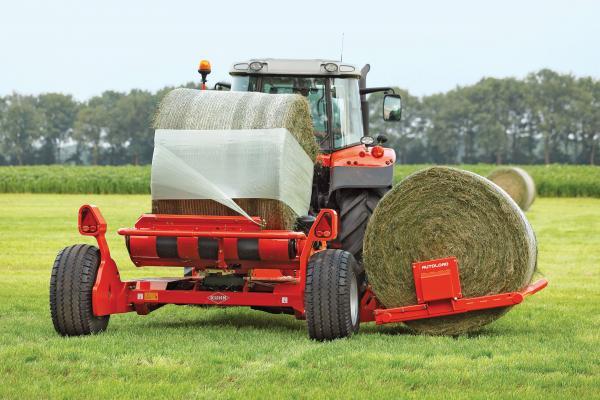
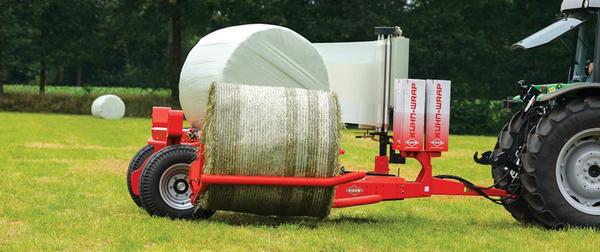
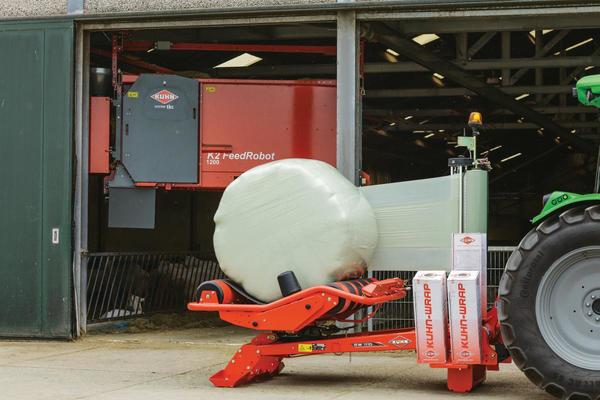
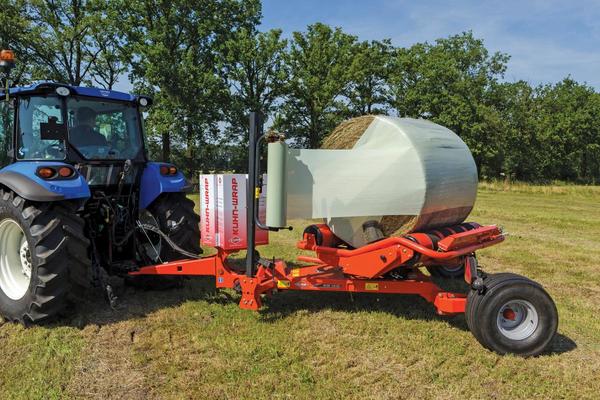
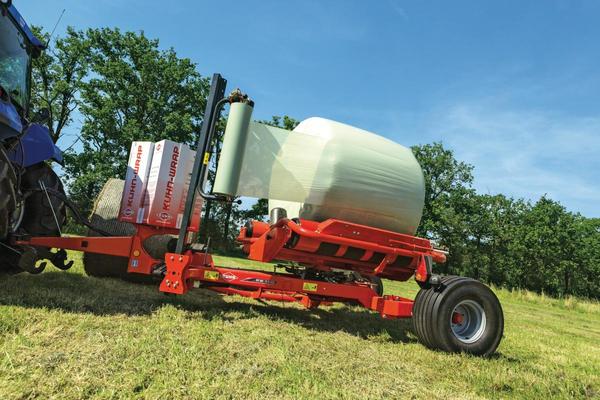
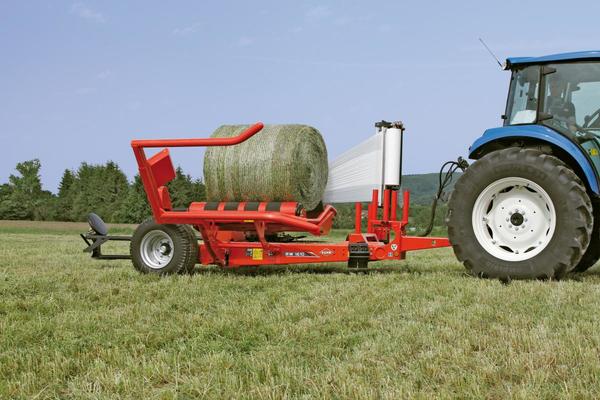
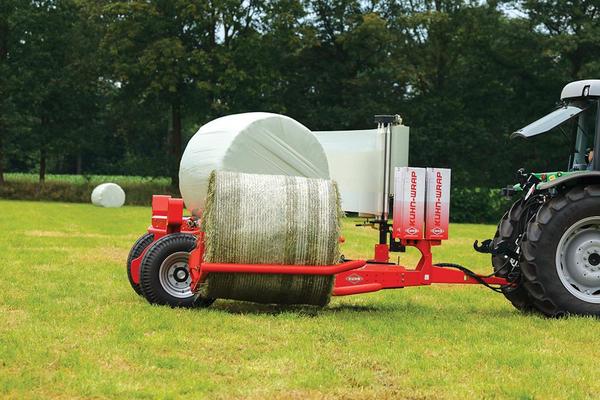
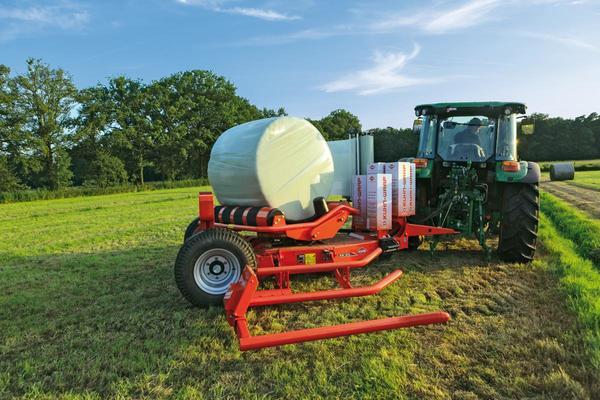
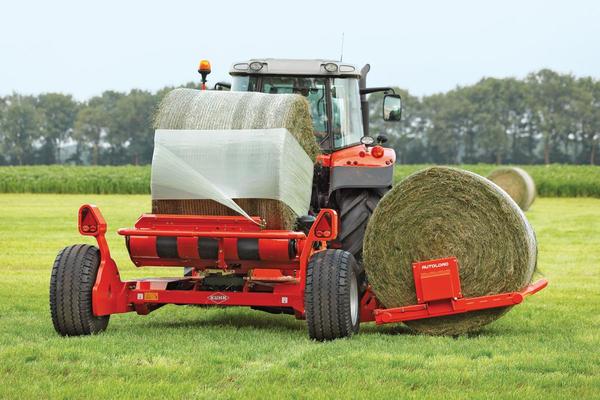
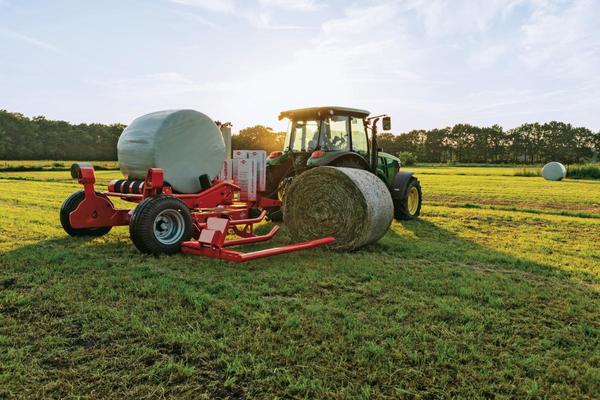
Make | Kuhn |
Model | RW 10 Series |
Type | Round Bale Wrappers |
Your Preferred Location
Description
Wrap round bales quickly and reliably with the KUHN RW 10 Series round bale wrappers. KUHN wrappers rotate bales evenly for exact film overlap and consistently and tightly-wrapped bales. The low-profile design provides gentle unloading of wrapped bales. Choose from two different control systems, manual or computer controlled, to best suit your personal preference. Our groundbreaking e-Twin models apply two layers of film at once to wrap bales in half the time of traditional models. The pre-stretchers, film cutters, wrapping table and low-profile chassis design make KUHN bale wrappers simple, easy-to-use, fast and efficient. KUHN bale wrappers, designed with you in mind, provide reliable performance to ensure optimum forage quality throughout the storage period.
The KUHN RW 1110 is a 3-point mounted, quick-hitch compatible model ideal for “wrap and stack” operations in the field or in the yard. Wrapping at the storage site means less risk of film damage and can be done by a one-man operation. The KUHN RW 1410 and 1610 are trailed, self-loading wrappers offering greater versatility. The RW 1410 will lift bales up to 5’ in diameter and 2,200 pounds, while the professional RW 1610 is capable of loading the heaviest bales up to 2,645 pounds.
The KUHN RW 1110 is a 3-point mounted, quick-hitch compatible model ideal for “wrap and stack” operations in the field or in the yard. Wrapping at the storage site means less risk of film damage and can be done by a one-man operation. The KUHN RW 1410 and 1610 are trailed, self-loading wrappers offering greater versatility. The RW 1410 will lift bales up to 5’ in diameter and 2,200 pounds, while the professional RW 1610 is capable of loading the heaviest bales up to 2,645 pounds.
Models
Round Turntable
The KUHN round bale turntable wrappers are equipped with two rollers and four wide-spaced belts. This design provides a deep and stable cradle for the bale on the wrapping turntable. The two large bale support rollers provide more stability and guidance. The four wide-spaced belts provide maximum traction and even rotation for the bale. Even bale rotation is vital to ensure the optimal film overlap for conservation and crop quality during storage.Patented, Conical Pre-Stretcher
The standard pre-stretchers, which hold a 30” (750 mm) roll, are made of aluminum to avoid build-up of tack from the film. Both outer ends of the aluminum rollers are cone-shaped to maintain the optimum width of the film and reduce the risk of film tear. The special ribbed profile of the aluminum rollers keeps air and water away from the film. The location of the pre-stretchers makes it very easy to change the film rolls. The standard pre-stretch of 70% is reached by a low-maintenance and low-noise gear transmission. An optional 60% pre-stretcher gear kit can be installed to change the standard pre-stretch to 60%, rather than 70%, to adapt to difficult wrapping conditions.e-Twin Technology
Besides a standard single stretch, KUHN introduces the all-new RW 10 series with patented* e-Twin system for excellent, cost efficient, fast wrapping. The innovative e-Twin technology enables wrapping via a unique combined pre-stretcher design with patented film distribution to save 50% on wrapping time and further film savings. The conical pre-stretch rollers have been positioned in such a way that the two 30" (750 mm) film wraps with 2/3 overlap are glued together providing a double layer before they leave the pre-stretcher unit. Optional on some of the wrappers is the auto film layer correct kit. The correct kit detects an empty or torn film roll and adjusts the required amount of table rotations to cover the bale with the required amount of layers. Unique Advantages of e-Twin: Save 50% wrapping time Further film saving achieved by increased pre stretch ratio Tighter wrapped bales increases the airtightness and so quality of feed - Extreme tear resistance under all circumstances - Available on manual and computer version with joystickFilm Cutters
Once the desired number of film layers have been applied, the film is then held firmly and cut. A spring-loaded or hydraulic high-grip film cutter holds and cuts the film automatically without the need for extra controls. The hydraulic high-grip film cutter, on the RW 1410 & RW 1610, allows you to adjust the cutting moment independent of the table tipping position, resulting in the shortest possible end string. It has a long stroke to help accommodate various bale lengths, and ensures a firm hold and a clean cut of the film in various weather conditions.Low-Profile Chassis Design
The KUHN trailed wrappers features a unique low-profile design ideal for stability when loading, wrapping or unloading a bale. The rear axle position results in a low table height eliminating the need for an active fall damper. There is constant weight transfer to the tractor that prevents up-and-down movements of the drawbar and prevents tractor wheel slippage when driving uphill with a bale on the table or loading arm. The bale can be dropped on the go for maximum output!Low Table Height
The low mounted table, on the mounted RW 1110, ensures a gentle bale discharge so there is no need for a fall damper. The low mounted height also allows easy replacement of the film rolls.Control Systems
Two different control systems are available dependent on model, and driver preferences: The manual version (M) is controlled with cable levers, and comes standard with the bale-and-wrap counter and autostop. The bale-and-wrap counter counts the film layers and total number of wrapped bales. The autostop function will automatically stop the wrapping table/satellite once the total number of film layers have been applied. This transforms a manually controlled wrapper into a semi-automatically controlled wrapper. The computer-controlled version (C) uses a control box that provides all the information and features for a fully automatic wrapping process. The integrated joystick automatically steers bale discharge, among other direct functions. The RW 1110 Computer version (C), with standard RF remote control, can be operated from a loader while using a power pack or second tractor for the oil- and power supply. This creates a one-man operation for loading, wrapping and stacking. The C version is standard fitted with automatic stop at the end of film/film tear, integrated bale and wrap counter, play/pause function and 90° loading position. The computer controlled version (C) on the RW 1410 uses a monitor, with an integrated joystick, that provides all the information and possibilities for automatic operation of the entire wrapping process. Automatic stop at the end of the film/film tear comes standard. The enhanced RW 1610 Computer controlled version (C), with integrated patented AutoLoad function, has increased overall efficiency and loading and wrapping capacity. The RF remote control with high distance safety control is optional.AutoLoad
The RW 1610 C can carry a second bale in the loading arm during wrapping. The AutoLoad function offers increased overall loading, wrapping capacity and efficiency. The patented AutoLoad function enables the operator to fully concentrate on the driving process, while the wrapping process is automatically started once the bale has been detected on the loading arm. Picking up a second bale with the loading arm, during the wrapping process for transport, is fully automated.SPECIFICATIONS
RW 1110 C | RW 1110 M | RW 1410 C | RW 1410 M | RW 1610 C | RW 1610 M | |
---|---|---|---|---|---|---|
Bale size (width x diameter) | 4' x (3-5)' (1.2 m x(0.9-1.5 m)) | 4' x (3-5)' (1.2 m x(0.9-1.5 m)) | 4' x (3-5)' (1.2 m x (0.9-1.5)m) | 4' x (3-5)' (1.2 m x (0.9-1.5)m) | 4' x (3-5)' (1.2 m x (0.9-1.5)m) | 4' x (3-5)' (1.2 m x (0.9-1.5)m) |
Maximum bale weight | 2,645 lbs (1,200 kg) | 2,645 lbs (1,200 kg) | 2,200 lbs (988 kg) | 2,200 lbs (988 kg) | Standard 2,200 lbs (998 kg) - optional 2,650 lbs (1,202 kg) | Standard 2,200 lbs (998 kg) - optional 2,650 lbs (1,202 kg) |
Transport width | 7'10" (2.4 m) | 7'10" (2.4 m) | 8'1" (2.7 m) | 8'1" (2.7 m) | 8'10" (2.7 m) | 8'10" (2.7 m) |
Transport height | 8'6'' (2.6 m) | 8'6'' (2.6 m) | 8'11'' (2.7 m) | 8'11'' (2.7 m) | 8'8'' (2.6 m) | 8'8'' (2.6 m) |
Hitch | Cat. 2 (quick hitch compatible as standard) | Cat. 2 (quick hitch compatible as standard) | ||||
Loading system | External | External | Loading arm | Loading arm | Standard autoload | Loading arm |
Ability to carry second bale on loading arm | N/A | N/A | Standard | Standard | ||
Wrapping table | 4 belts + 2 rollers | 4 belts + 2 rollers | 4 belts + 2 rollers | 4 belts + 2 rollers | 4 belts + 2 rollers | 4 belts + 2 rollers |
Bale support roller | 2 adjustable rollers | 2 adjustable rollers | 2 adjustable rollers | 2 adjustable rollers | 2 adjustable rollers | 2 adjustable rollers |
Control | (C) Computer controlled (VT 30) | (M) Manual 2 lever cable controlled | (C) Computer controlled (VT 30) | (M) Manual 3 lever cable controlled | (C) Computer controlled (VT 30) | (M) Manual 3 lever controlled |
Semi-automatic operation of (M) version by bale and wrap counter and automatic table stop | - | Standard | - | Standard | ||
Automatic stop by end of film / tear | Standard | - | Standard | - | Standard | - |
RF remote control (rechargeable) | Standard | - | Optional | - | Optional | - |
Fully automatic film cutter | Sure grip as standard | Sure grip as standard | Standard | Standard | Standard | Standard |
Film pre-stretcher | Standard 30" (75 cm) - optional kit for 20" (52 cm) |
Standard 30" (75 cm) - optional kit for 20" (52 cm) |
Standard 30" (76 cm) - optional kit for 20" (51 cm) | Standard 30" (76 cm) - optional kit for 20" (51 cm) | Standard 30" (76 cm) - optional kit for 20" (51 cm) | Standard 30" (76 cm) - optional kit for 20" (51 cm) |
Pre-stretch ratio | Approx. 70% standard - Optional 60% |
Approx. 70% standard - Optional 60% |
Approx. 70% standard / 90% E-twin - Optional 60 % |
Approx. 70% standard / 90% E-twin - Optional 60 % |
Approx. 70% standard / 90% E-twin - Optional 60% |
Approx. 70% standard / 90% E-twin - Optional 60% |
Required tractor hydraulic connections | 1 SA with free return or 1 DA | 1 SA with free return or 1 DA | 1 SA with free return or 1 DA | 1 SA with free return or 1 DA | 1 SA with free return or 1 DA | 1 SA with free return or 1 DA |
Output and pressure required | 7 gpm at 2,200 psi | 7 gpm at 2,200 psi | 7 gpm at 2,200 psi | 7 gpm at 2,200 psi | 7 gpm at 2,200 psi | 7 gpm at 2,200 psi |
Road lights | Optional | Optional | Standard | Standard | ||
Tires | 10.0/80-12 | 10.0/80-12 | Standard 380/55x17 | Standard 380/55x17 | ||
Ability to turn wheels inside for road transport | Right side swivels, left side is fixed | Right side swivels, left side is fixed | N/A | N/A | ||
Machine net weight | 1,985 lbs (900 kg) | 1,985 lbs (900 kg) | 2,200 lbs (998 kg) | 2,200 lbs (998 kg) | 3,285 lbs (1,490 kg) | 3,285 lbs (1,490 kg) |
Links
Copy Set
Round Turntable
The KUHN round bale turntable wrappers are equipped with two rollers and four wide-spaced belts. This design provides a deep and stable cradle for the bale on the wrapping turntable. The two large bale support rollers provide more stability and guidance. The four wide-spaced belts provide maximum traction and even rotation for the bale. Even bale rotation is vital to ensure the optimal film overlap for conservation and crop quality during storage.
Patented, Conical Pre-Stretcher
The standard pre-stretchers, which hold a 30” (750 mm) roll, are made of aluminum to avoid build-up of tack from the film. Both outer ends of the aluminum rollers are cone-shaped to maintain the optimum width of the film and reduce the risk of film tear. The special ribbed profile of the aluminum rollers keeps air and water away from the film. The location of the pre-stretchers makes it very easy to change the film rolls. The standard pre-stretch of 70% is reached by a low-maintenance and low-noise gear transmission. An optional 60% pre-stretcher gear kit can be installed to change the standard pre-stretch to 60%, rather than 70%, to adapt to difficult wrapping conditions.
e-Twin Technology
Besides a standard single stretch, KUHN introduces the all-new RW 10 series with patented* e-Twin system for excellent, cost efficient, fast wrapping. The innovative e-Twin technology enables wrapping via a unique combined pre-stretcher design with patented film distribution to save 50% on wrapping time and further film savings. The conical pre-stretch rollers have been positioned in such a way that the two 30" (750 mm) film wraps with 2/3 overlap are glued together providing a double layer before they leave the pre-stretcher unit. Optional on some of the wrappers is the auto film layer correct kit. The correct kit detects an empty or torn film roll and adjusts the required amount of table rotations to cover the bale with the required amount of layers. Unique Advantages of e-Twin: Save 50% wrapping time Further film saving achieved by increased pre stretch ratio Tighter wrapped bales increases the airtightness and so quality of feed - Extreme tear resistance under all circumstances - Available on manual and computer version with joystick
Film Cutters
Once the desired number of film layers have been applied, the film is then held firmly and cut. A spring-loaded or hydraulic high-grip film cutter holds and cuts the film automatically without the need for extra controls. The hydraulic high-grip film cutter, on the RW 1410 & RW 1610, allows you to adjust the cutting moment independent of the table tipping position, resulting in the shortest possible end string. It has a long stroke to help accommodate various bale lengths, and ensures a firm hold and a clean cut of the film in various weather conditions.
Low-Profile Chassis Design
The KUHN trailed wrappers features a unique low-profile design ideal for stability when loading, wrapping or unloading a bale. The rear axle position results in a low table height eliminating the need for an active fall damper. There is constant weight transfer to the tractor that prevents up-and-down movements of the drawbar and prevents tractor wheel slippage when driving uphill with a bale on the table or loading arm. The bale can be dropped on the go for maximum output!
Low Table Height
The low mounted table, on the mounted RW 1110, ensures a gentle bale discharge so there is no need for a fall damper. The low mounted height also allows easy replacement of the film rolls.
Control Systems
Two different control systems are available dependent on model, and driver preferences: The manual version (M) is controlled with cable levers, and comes standard with the bale-and-wrap counter and autostop. The bale-and-wrap counter counts the film layers and total number of wrapped bales. The autostop function will automatically stop the wrapping table/satellite once the total number of film layers have been applied. This transforms a manually controlled wrapper into a semi-automatically controlled wrapper. The computer-controlled version (C) uses a control box that provides all the information and features for a fully automatic wrapping process. The integrated joystick automatically steers bale discharge, among other direct functions. The RW 1110 Computer version (C), with standard RF remote control, can be operated from a loader while using a power pack or second tractor for the oil- and power supply. This creates a one-man operation for loading, wrapping and stacking. The C version is standard fitted with automatic stop at the end of film/film tear, integrated bale and wrap counter, play/pause function and 90° loading position. The computer controlled version (C) on the RW 1410 uses a monitor, with an integrated joystick, that provides all the information and possibilities for automatic operation of the entire wrapping process. Automatic stop at the end of the film/film tear comes standard. The enhanced RW 1610 Computer controlled version (C), with integrated patented AutoLoad function, has increased overall efficiency and loading and wrapping capacity. The RF remote control with high distance safety control is optional.
AutoLoad
The RW 1610 C can carry a second bale in the loading arm during wrapping. The AutoLoad function offers increased overall loading, wrapping capacity and efficiency. The patented AutoLoad function enables the operator to fully concentrate on the driving process, while the wrapping process is automatically started once the bale has been detected on the loading arm. Picking up a second bale with the loading arm, during the wrapping process for transport, is fully automated.
SPECIFICATIONS
RW 1110 C | RW 1110 M | RW 1410 C | RW 1410 M | RW 1610 C | RW 1610 M | |
---|---|---|---|---|---|---|
Bale size (width x diameter) | 4' x (3-5)' (1.2 m x(0.9-1.5 m)) | 4' x (3-5)' (1.2 m x(0.9-1.5 m)) | 4' x (3-5)' (1.2 m x (0.9-1.5)m) | 4' x (3-5)' (1.2 m x (0.9-1.5)m) | 4' x (3-5)' (1.2 m x (0.9-1.5)m) | 4' x (3-5)' (1.2 m x (0.9-1.5)m) |
Maximum bale weight | 2,645 lbs (1,200 kg) | 2,645 lbs (1,200 kg) | 2,200 lbs (988 kg) | 2,200 lbs (988 kg) | Standard 2,200 lbs (998 kg) - optional 2,650 lbs (1,202 kg) | Standard 2,200 lbs (998 kg) - optional 2,650 lbs (1,202 kg) |
Transport width | 7'10" (2.4 m) | 7'10" (2.4 m) | 8'1" (2.7 m) | 8'1" (2.7 m) | 8'10" (2.7 m) | 8'10" (2.7 m) |
Transport height | 8'6'' (2.6 m) | 8'6'' (2.6 m) | 8'11'' (2.7 m) | 8'11'' (2.7 m) | 8'8'' (2.6 m) | 8'8'' (2.6 m) |
Hitch | Cat. 2 (quick hitch compatible as standard) | Cat. 2 (quick hitch compatible as standard) | ||||
Loading system | External | External | Loading arm | Loading arm | Standard autoload | Loading arm |
Ability to carry second bale on loading arm | N/A | N/A | Standard | Standard | ||
Wrapping table | 4 belts + 2 rollers | 4 belts + 2 rollers | 4 belts + 2 rollers | 4 belts + 2 rollers | 4 belts + 2 rollers | 4 belts + 2 rollers |
Bale support roller | 2 adjustable rollers | 2 adjustable rollers | 2 adjustable rollers | 2 adjustable rollers | 2 adjustable rollers | 2 adjustable rollers |
Control | (C) Computer controlled (VT 30) | (M) Manual 2 lever cable controlled | (C) Computer controlled (VT 30) | (M) Manual 3 lever cable controlled | (C) Computer controlled (VT 30) | (M) Manual 3 lever controlled |
Semi-automatic operation of (M) version by bale and wrap counter and automatic table stop | - | Standard | - | Standard | ||
Automatic stop by end of film / tear | Standard | - | Standard | - | Standard | - |
RF remote control (rechargeable) | Standard | - | Optional | - | Optional | - |
Fully automatic film cutter | Sure grip as standard | Sure grip as standard | Standard | Standard | Standard | Standard |
Film pre-stretcher | Standard 30" (75 cm) - optional kit for 20" (52 cm) |
Standard 30" (75 cm) - optional kit for 20" (52 cm) |
Standard 30" (76 cm) - optional kit for 20" (51 cm) | Standard 30" (76 cm) - optional kit for 20" (51 cm) | Standard 30" (76 cm) - optional kit for 20" (51 cm) | Standard 30" (76 cm) - optional kit for 20" (51 cm) |
Pre-stretch ratio | Approx. 70% standard - Optional 60% |
Approx. 70% standard - Optional 60% |
Approx. 70% standard / 90% E-twin - Optional 60 % |
Approx. 70% standard / 90% E-twin - Optional 60 % |
Approx. 70% standard / 90% E-twin - Optional 60% |
Approx. 70% standard / 90% E-twin - Optional 60% |
Required tractor hydraulic connections | 1 SA with free return or 1 DA | 1 SA with free return or 1 DA | 1 SA with free return or 1 DA | 1 SA with free return or 1 DA | 1 SA with free return or 1 DA | 1 SA with free return or 1 DA |
Output and pressure required | 7 gpm at 2,200 psi | 7 gpm at 2,200 psi | 7 gpm at 2,200 psi | 7 gpm at 2,200 psi | 7 gpm at 2,200 psi | 7 gpm at 2,200 psi |
Road lights | Optional | Optional | Standard | Standard | ||
Tires | 10.0/80-12 | 10.0/80-12 | Standard 380/55x17 | Standard 380/55x17 | ||
Ability to turn wheels inside for road transport | Right side swivels, left side is fixed | Right side swivels, left side is fixed | N/A | N/A | ||
Machine net weight | 1,985 lbs (900 kg) | 1,985 lbs (900 kg) | 2,200 lbs (998 kg) | 2,200 lbs (998 kg) | 3,285 lbs (1,490 kg) | 3,285 lbs (1,490 kg) |