Hagie DTS10 Hagie™ Self-Propelled Sprayer
Sprayers - Hagie Self-Propelled
Your Preferred Location
Features
-
Solution Capacity: 1,000 gallons (3,800 L)
-
Transport Speed: 30 mph (45 km/h)
-
Boom Sections: 5
-
Application Speed: 20 mph (32 km/h)
-
Boom Width: up to 90 feet (27 m)
-
Engine hp: 225 (167 kW)
Specifications
Additional information - Date collected: |
08-May-2018 |
Boom - Automatic boom height: |
NORAC |
Boom - Boom length options: |
18/24 and 18/27 m 60/80 and 60/90 ft |
Boom - Boom sections: |
Seven sections for boom widths - 18/24 and 18/27 m 60/80 and 60/90 ft |
Boom - Breakaway width: |
For 27-m (90-ft) booms - 3 m 10 ft |
Boom - Ground height adjustment: |
58 to 257 cm 23 to 101 in. |
Boom - Plumbing material: |
Stainless steel |
Chassis - Crop clearance with standard tires: |
182 cm 72 in. |
Chassis - Dry compatible: |
No |
Chassis - Flotation tires: |
540/65R30 |
Chassis - Front tires: |
380/80R38 or 320/80R42 |
Chassis - Hydraulic tread adjust: |
Optional |
Chassis - Ladder raise/lower: |
Hydraulic |
Chassis - Parking brake: |
Integrated in final drives |
Chassis - Primary brakes: |
Drive system dynamic braking |
Chassis - Rear tires: |
380/80R38 or 320/80R42 |
Chassis - Suspension: |
Independent air-ride |
Chassis - Total weight with 80-ft boom: |
9,162 kg 20,200 lb |
Chassis - Total weight with 90-ft boom: |
9,307 kg 20,520 lb |
Chassis - Turning radius: |
5.9 m 19.4 ft |
Chassis - Wheel base: |
353 cm 139 in. |
Chassis - Wheel tread spacing: |
305 to 406 cm 120 to 160 in. |
Drivetrain - Drive: |
Full-time four-wheel drive (4WD) |
Drivetrain - Hydraulic reservoir capacity: |
95 L 25 gal. |
Drivetrain - Shifting: |
Dual range speed control with incremental speed adjustment within each range |
Drivetrain - Spray speed range: |
0.8 to 32 km/h 0.5 to 20 mph |
Drivetrain - Transport speed, maximum: |
48 km/h 30 mph |
Drivetrain - Type: |
Hydrostatic |
Engine - Alternator: |
200 amp |
Engine - Diesel exhaust fluid (DEF) tank capacity: |
37.9 L 10 gal. |
Engine - Displacement: |
6.7 L 409 cu in. |
Engine - Emissions: |
Final Tier 4 (FT4) |
Engine - Fuel tank capacity: |
378.5 L 100 gal. |
Engine - Number of cylinders: |
Six |
Engine - Peak rated power: |
167 kW 225 hp |
Key Specs - Boom length options/Material: |
18/24 and 18/27 m 60/80 and 60/90 ft |
Key Specs - Crop clearance with standard tires: |
182 cm 72 in. |
Key Specs - Engine: |
Peak rated power 167 kW 225 hp |
Key Specs - Rinse tank capacity: |
208 L 55 gal. |
Key Specs - Solution system - Capacity: |
Two tanks - per tank - 1890 L 500 gal. |
Key Specs - Spray speed range: |
0.8 to 32 km/h 0.5 to 20 mph |
Key Specs - Suspension: |
Independent air-ride |
Key Specs - Transport speed, maximum: |
48 km/h 30 mph |
Options - Air compressor: |
Onboard air |
Options - Foam marker capacity: |
11.35 L 3 gal. |
Solution system - Automatic section control: |
Optional |
Solution system - Boom strainer: |
Optional 80 mesh |
Solution system - Capacity: |
Per tank - 1890 L 500 gal. |
Solution system - Chemical eductor: |
Optional |
Solution system - Chemical eductor capacity (size): |
30.3 L 8 gal. |
Solution system - Fill location: |
Rear |
Solution system - Flow meter size: |
5.8 cm 2 in. |
Solution system - Pressure strainer: |
50 mesh |
Solution system - Quick fill size: |
Quick-fill connection - 5.1 cm 2 in. |
Solution system - Rate control make: |
John Deere Raven / Ag Leader optional |
Solution system - Rinse tank capacity: |
208 L 55 gal. |
Solution system - Solution system control: |
John Deere Raven/Ag Leader - optional |
Solution system - Tank material: |
Poly |
Solution tank, pump, and pump switch
Solution tank
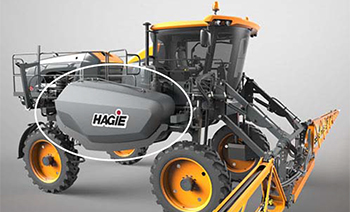
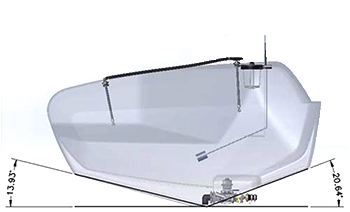
Two 1892-L (500-gal.) polyethylene tanks are mounted on tank cradles on each side of the machine. The solution tank design allows the sump to drain on a 30 percent grade and is equipped with a spinball rinse system. A mechanical sight gauge is located on top of each solution tank to visually check the solution level at all times.
Solution pump

The Hypro® 9306C-HM1C solution pump (located beneath the center of the machine) is a centrifugal-type hydraulically driven pump that is controlled by the solution pump control valve and the spray system console. It comes with silicon-carbide seals.
The solution pump draws solution out of the tank at the rate determined during calibration. It dispenses solution through the many valves and hoses that make up the spray system and also dispenses fluids through the agitation and rinse systems.
Solution pump switch
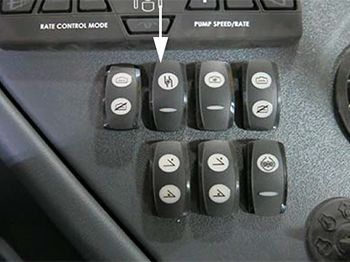
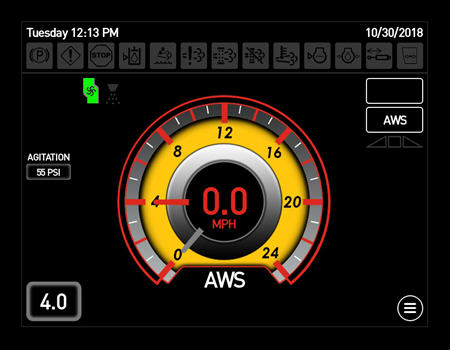
The solution pump switch is located on the side console and is used to turn the solution pump on and off.
NOTE: When the solution pump is on, a solution pump indicator (located on the machine display home page - field mode) will illuminate.
Hypro is a trademark of Pentair Flow Technologies, LLC.
DTS10 cab and controls overview
Front console
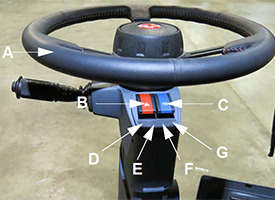
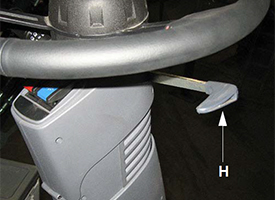
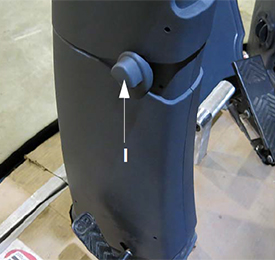
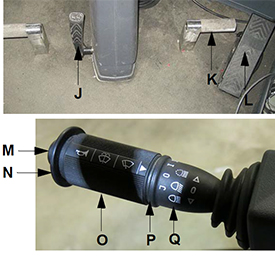
Location (image) | Component | Description/notes |
A | Steering wheel | Optional premium leather-wrapped steering wheel |
B | Hazard/warning lights switch | --- |
C | Highway/warning lights switch | --- |
D | Turn signal indicator | Left-hand side |
E | Highway running lights indicator | --- |
F | High beams indicator | --- |
G | Turn signal indicator | Right-hand side |
H | Steering wheel telescope adjust handle | Available only if equipped with this option |
I | Steering column tilt adjust button | Knee angle Available only if equipped with this option |
J | Steering column release pedal | --- |
K | Operator foot pegs | Two pegs Available only if equipped with this option |
L | Deceleration (decel) pedal | --- |
M | Horn | --- |
N | Windshield washer | --- |
O | Turn signal lever | --- |
P | Windshield wiper speed | --- |
Q | High beams (brights) | --- |
Side console
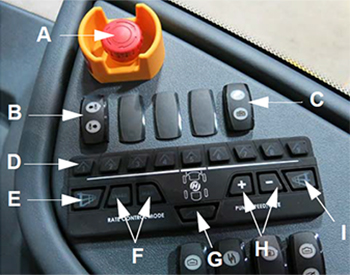
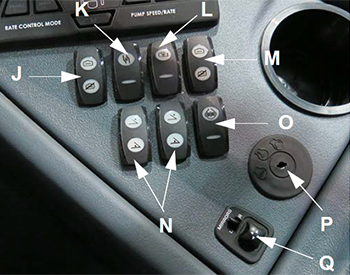
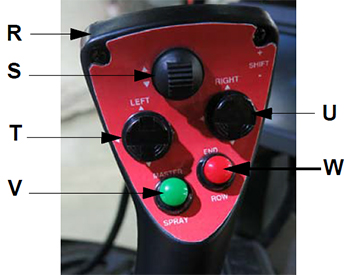
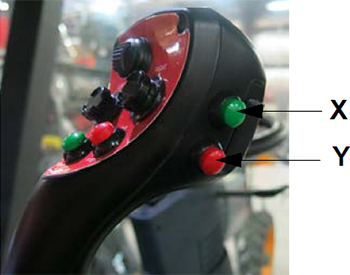
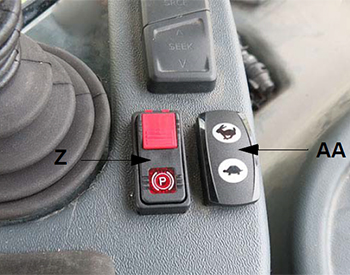
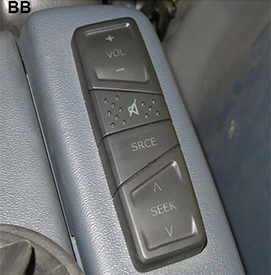
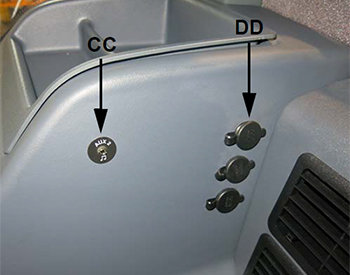
Location (image) | Component | Description/notes |
A | Emergency stop (e-stop) switch | The e-stop switch provides a quick method for stopping the engine in an emergency situation. |
B | Foam marker switch (if equipped) | The foam marker switch controls foam application on both sides of the machine. |
C | Rinse switch | The rinse switch is used to rinse the solution tank and spray booms. |
D | Boom solution valve switches | The boom solution valve switches each control a valve located on the boom or transom. The valves control the flow of the solution through the boom. |
E | Fence row switch (left-hand side) | The fence row switches are used in the selection of either the right or left fence row spray nozzle. |
F | Rate control switches | The rate control switches control the rate in which solution is applied through the spray booms by either the rate controller (enable) or operator-controlled spray rate (manual). |
G | Rear nozzle switch | The rear nozzle switch controls the two rear nozzles (located behind the rear tires). |
H | Pump speed and rate switches | The pump speed/rate switches allow the operator to increase or decrease flow rate through the spray system. |
I | Fence row switch (right-hand side) | --- |
J | Main tank valve switch (left-hand side) | The main tank valve switch controls the solution tank valve. This switch must be in the on (open) position for spray application. |
K | Solution pump switch | The solution pump switch is used to turn the solution pump on or off. |
L | Agitation valve switch | The agitation valve switch controls the rate of flow through the agitation system. |
M | Main tank valve switch (right-hand side | --- |
N | Boom extension switches (left/right outer fold) | The boom extension switches are used to extend or retract the outer boom extensions. |
O | Traction valve switch | --- |
P | Ignition switch | --- |
Q | Power mirror switch (if equipped) | The power mirror switch allows vertical or horizontal adjustment of the electric side-view mirrors by pressing the switch in the desired position. |
R | Hydrostatic drive control handle | The hydrostatic drive control handle controls the direction of the machine and the speed in which it travels. It is also used to control the spray booms, master spray, end row management, and shift up/down speeds. |
S | Transom switch (up/down) | The transom switch is used to raise and lower the main lift. |
T | Right-hand boom switch | The left- and right-hand boom switches are used to raise, lower, extend, and retract the spray booms. |
U | Left-hand boom switch | The left- and right-hand boom switches are used to raise, lower, extend, and retract the spray booms. |
V | Master spray switch | The master spray switch activates the boom solution valves. |
W | End row management switch | The end-row management switch is a programmable switch that enables various functions (i.e. all-wheel steer, auto steer, master spray, and NORAC® enable) when the switch is depressed. End-row management settings are programmed through the machine display. |
X | Shift up switch | The shift up/down switches are used for speed range selection. |
Y | Shift down switch | The shift up/down switches are used for speed range selection. |
Z | Parking brake switch | The parking brake switch is used to engage and disengage the parking brake, as well as extend and retract the ladder. |
AA | Throttle switch | The throttle switch is used to control engine speed (rpm). |
BB | Remote stereo controls | The remote stereo controls are conveniently located to control the stereo (volume, mute, source, and seek). |
CC | 12-V power ports | Four power ports are provided for the connection of additional items (such as radios and computer equipment). |
DD | Two auxiliary audio input connections | The auxiliary audio input allows connection of a personal iPod® device or MP3 player. |
Overhead monitors and controls
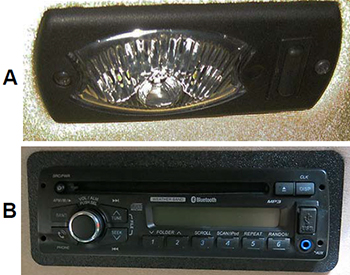
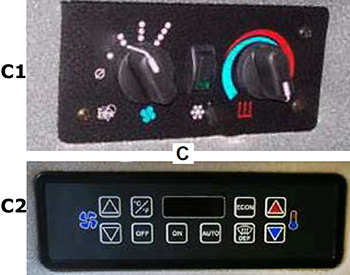
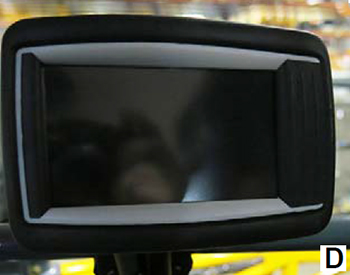

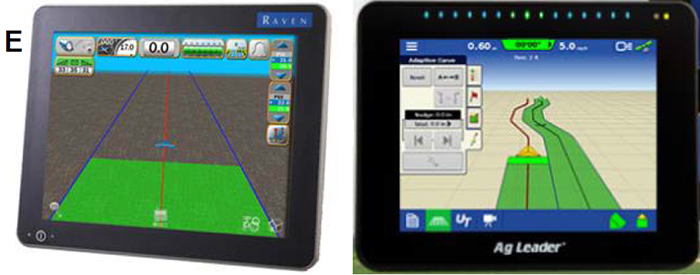
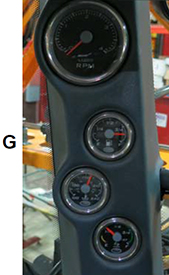
Location (image) | Component | Description/notes |
A | Courtesy/interior work light | The courtesy light comes on automatically when the cab door is opened. The interior work light is activated by manually pressing the interior work light switch (located on the light housing). |
B | Stereo (if equipped) | The stereo features with an AM/FM tuner, weatherband broadcasting, CD player, MP3 player, USB/iPod controls, and Bluetooth® wireless system (if equipped). |
C | Climate controls | The climate controls allow the operator to set and maintain desired cab temperature. Vents are placed throughout the cab to keep air circulating and to maintain clear windows throughout the cab. |
D | NORAC monitor (if equipped) | The NORAC monitor controls the automatic boom leveling system. |
E | Spray system console | The spray system is controlled by the spray system console and the solution pump control valve. The system receives data and automatically makes adjustments based on the target rate of application set by the operator. |
F | Machine display | The machine display is the central control center of the machine. It controls many of the machine’s electronically driven functions (i.e. machine drive, AWS, attachment operation, tread adjustment, spray systems, lights, diagnostics, etc.). |
G | Machine gauges | The machine gauge panel on the A-post is conveniently located for viewing engine rpm, fuel level, engine coolant temperature, and engine aftertreatment level (if equipped). |
NORAC is a trademark of NORAC Systems International, Inc. iPod is a trademark of Apple, Inc. Bluetooth is a trademark of Bluetooth SIG, Inc.
Frame and axles
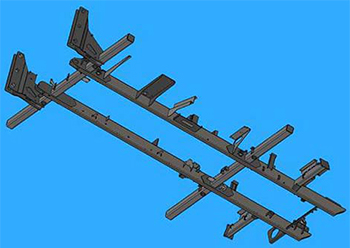
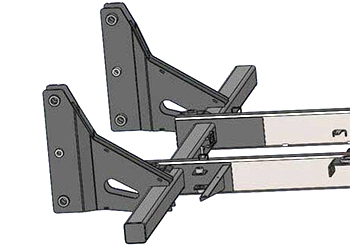
The DTS10 Sprayer mainframe design features horizontal cross-through axle tubes, as well as boom and platform mounts on weldment.
- 360.7-cm (142-in.) mainframe width
- 182.9-cm (72-in.) ground clearance
John Deere Connected Support™ prevents downtime and efficiently resolves issues with revolutionary technology-based solutions
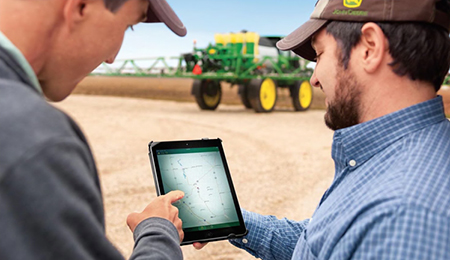
When you buy John Deere equipment, you expect reliability. You also know that problems can happen, and a product is only as good as the support behind it. That’s why John Deere equipment is prepared with technology that senses potential issues and can alert you and your dealer promptly—in the cab or anywhere you are.
John Deere Connected Support is a revolutionary change to support that leverages technology and the connectivity of JDLink™ telematics to prevent downtime and resolve problems faster. These tools decrease downtime by an average of 20 percent, enabling faster responses to unexpected problems and reducing technician trips to your machine. For some issues, unplanned downtime can even be prevented altogether through prediction of the issue.
With your permission, John Deere Connected Support:
- Keeps you running by monitoring machine health and promptly alerting you and your dealer of issues
- Saves time by remotely viewing in-cab displays, reducing trips to the machine
- Reduces or even eliminates technician trips to a machine through remote diagnostic and remote software reprogramming capabilities
- Connects experts with the information needed to respond to downtime faster and prevent it altogether
With more than a decade of experience leveraging connectivity to solve problems, no one else has the experience, tools, and knowledge to keep you running as John Deere and your John Deere dealer can. Connected Support is an in-base feature on all John Deere products with factory- or field-installed JDLink.
DTS10 spray booms

The spray booms are controlled by an electrohydraulic system. This system consists of operator-manipulated switches (located on the side console and the hydrostatic drive control handle) and hydraulic cylinders (attached to the booms), which provide lift, level, and horizontal extension.
Hydraulically folding the extensions of an 18.3- or 24.4-m (60- or 80-ft) or 18.3- or 27.4-m (60- or 90-ft) spray boom and shutting off the outer sections essentially turns it into an 18.3-m (60-ft) spray boom. The wet boom connections feature with ARAG® EasyFit fittings with an o-ring seal and are 13-mm (0.5-in.) schedule 5 pipe-fed from one end with a 25-mm (1-in.) hose.
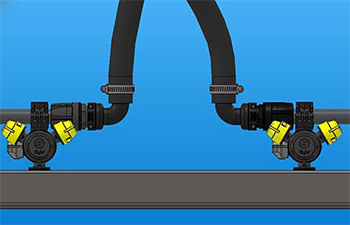
Boom configurations
Sprayer model |
Boom location |
Minimum boom width |
Maximum boom width |
Number of boom sections |
Wet boom nozzle spacing |
DTS10 | Front | 18.3 or 24.4 m (60 or 80 ft) |
18.3 or 27.4 m (60 or 90 ft) |
Seven | Standard - 38 cm (15 in.) Optional - 51 cm (20 in.) |
ARAG is a trademark of ARAG S.r.l.
Hagie™ DTS Series engines
6.7-L (408.9-cu in.) Cummins® QSB engine
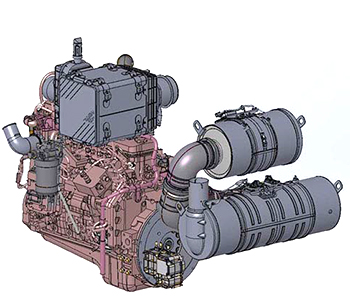
The Hagie DTS10 is powered by a 6.7-L (408.9-cu in.) Cummins QSB diesel engine providing 165-kW (225-hp) using an emissions-compliant Final Tier 4 (FT4) configuration. This 6.7-L (408.9-cu in.) engine is electronic with an air-to-air cooler and turbocharger.
The FT4 engine requires ultra-low sulfur diesel (ULSD).
Engine location
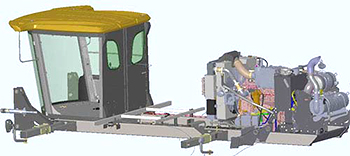
The rear-mounted engine keeps constant weight to offset the spray boom and leaves space in the center of machine for the varying weight of fuel and rinse tanks. This allows for better coolant airflow and reduction of cab noise.
Engine exhaust
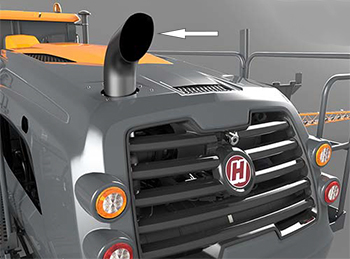
The engine exhaust is located at the rear of the machine. This helps to reduce interior cab and noise vibration.
Cummins is a trademark of Cummins, Inc. Hagie is a trademark of Hagie Manufacturing Company, LLC and similar to John Deere branded equipment, Deere will also support Hagie equipment.