John Deere 1795 16Row Split 31 or 32 Planter
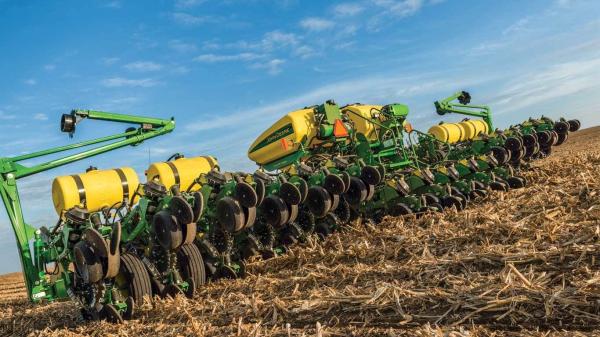
Make | John Deere |
Model | 1795 16Row Split 31 or 32 |
Type | Drawn Planters |
Your Preferred Location
Description
- 40-ft. toolbar with 16 rows on 30-in. spacing
- Can also be configured as 31-row split row in 15-in. spacing or even row of 32 rows
- Available with optional ExactEmerge™ or MaxEmerge™ 5e row unit or standard in mini-hopper MaxEmerge™ 5 row unit
- 3-section frame flexes 15 degrees up & down with narrow transport of 12 ft.
Models
Precise liquid fertilizer placement with ExactRate™ fertilizer system
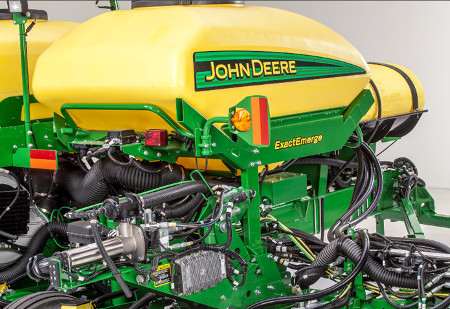
The ExactRate liquid fertilizer system is a factory-installed solution that provides you with accurate nutrient placement during planting. Previously, you would have to deal with the inconvenience of cumbersome aftermarket systems for a hydraulically driven variable-rate solution. With ExactRate, John Deere delivers a complete planting solution for liquid fertilizer users. You can choose between in-furrow or offset delivery methods. This system delivers:
- Up to 20 percent more accurate nutrient placement in a turn compared to a non-turn compensating systems
- 1 to 12 percent (4.3 percent on average) reduction in inputs through row-by-row section control
- Ability to run up to 16.1 km/h (10 mph)
- Closed-loop speed and rate change compensation
- Full integration into the 4600 CommandCenter™ and 4640 Universal Display
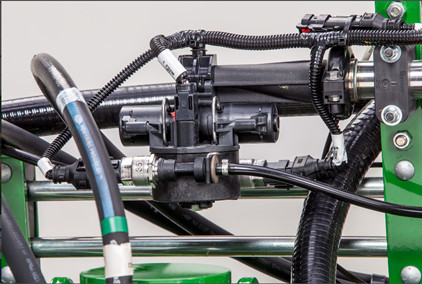
The ExactRate liquid fertilizer system is designed to take full advantage of the capabilities of ExactEmerge™ and MaxEmerge™ 5e planters. This factory-installed liquid fertilizer system delivers the same value as your electric drive planter including working at speeds faster than the traditional 8.05 km/h (5 mph), turn compensation, and row-by-row section control, all while accurately compensating for varying rates and speed changes. Additional features include row-by-row flow detection, as-applied documentation, and variable-rate capabilities, providing operators full integration into the 4600 CommandCenter or 4640 Universal Display.
Fertilizer flows from the tank to the pump, through a strainer and boom isolation valve, through a central flowmeter, and out to each nozzle body and row-unit for accurate delivery. The system is closed loop, meaning the pump and nozzle body duty cycle both adjust based on feedback received from the pressure sensor and central flowmeter. This design helps maintain an accurate application rate.
NOTE: ExactRate is not recommended for products that require agitation to maintain suspension.
Pump
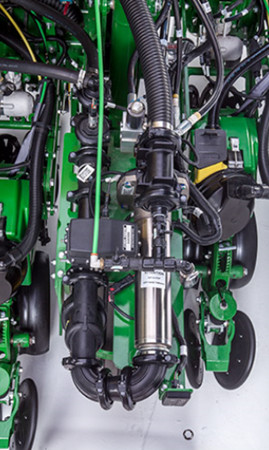
Instead of a tire-contact drive, a hydraulically driven centrifugal pump eliminates chain and sprocket adjustments to provide more speed flexibility over the entire rate range. This pump allows for a wide range of rate capabilities as well as strong durability. The wet seal design helps protect the pump if it is accidentally run dry for a short time.
Strainer
A strainer helps collect suspended particles and prevent them from causing blockages in the distribution system and nozzle bodies.
Boom isolation valve
The valve prevents the tank from draining out if there is a leak in the distribution system. If the pump is on, the valve opens to allow flow. When the pump is off, the valve closes.
Central flowmeter and pump pressure sensor
The central flowmeter and pump pressure sensor provide the rate control system feedback on flow and pressure to ensure an accurate application rate across the entire planter width. The flowmeter also supplies the as-applied rate data.
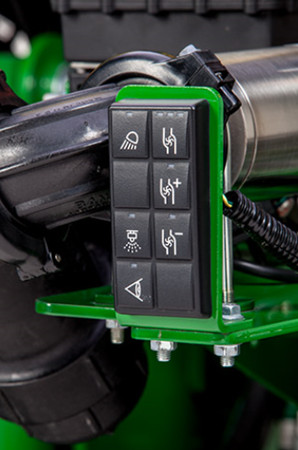
Just like on the sprayers, the keypad at the rear of the machine lets you conveniently perform a nozzle flow check to ensure product is coming out of each row before going to the field.
Direct injection
The ExactRate liquid fertilizer system does not have direct injection capabilities on the product being applied. If direct injection is needed on the secondary product, an additional rate controller is required.
NOTE: ExactRate system and John Deere Rate Controller 2000 with Raven ICD Direct Injection system is supported. ExactRate system and GreenStar Rate Controller with Raven ISO Direct Injection system is not supported.
Distribution system and nozzle body
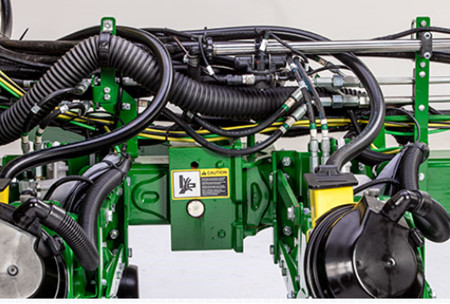
The 2.5-cm (1-in.) stainless-steel distribution lines not only reduce corrosion, they also provide a clean integrated look. The distribution system is pressure tested at the factory to reduce the risk of leaks.
John Deere has leveraged ExactApply™ technology and capabilities from the sprayers to enable row-by-row section control and turn compensation that matches the high-performance planters. With ExactRate, there are no orifice changes for rate or speed adjustments, saving you time and effort while limiting exposure to product. Pulse-width modulation technology varies duty cycle (opening and closing of the valve) in the nozzle bodies in conjunction with flow and pressure measured from central flowmeter and pressure sensor controlling the system pump. The ExactRate liquid fertilizer system uses one nozzle body for two rows, limiting the number of parts and complexity on each machine. While you’re in the cab, you’ll be able to keep an eye on each row with flow detection integrated into the Gen 4 display. The system will warn you if it detects a variance in an individual row’s flow. A pressure sensor integrated into the nozzle body will detect a flow reduction or overapplication on the row.
Rate Controller
The ExactRate liquid fertilizer system is compatible with the John Deere Rate Controller 2000 and GreenStar™ Rate Controller if a producer wants to apply a second product using a separate distribution system.
ExactRate app on Gen 4
Easily adjust target rate and speed without leaving your seat. With turn compensation, inner and outer rates are automatically adjusted to maintain consistent application across the full width of the planter. This ultimately reduces the risk of seed burn by over application (turn compensations require a global positioning system [GPS] receiver). Another helpful feature is row-by-row section control for reduced overlap on headlands and waterways. Gen 4 Documentation creates as-applied maps showing what product was applied where, providing accurate record-keeping.
Dual 56-V electric motors for ExactEmerge™ row-units
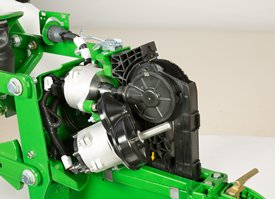
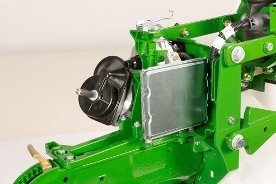
Two 56-V brushless electric motors provide ExactEmerge the upper hand over any other row-unit on the market. One motor controls the high-performance meter and the other powers the BrushBelt™ delivery system. Both feature a closed loop system ensuring they operate at the correct rpm.
The motor is controlled at a rate of 200 times per second and a decision is made every 5 milliseconds. The controller also keeps each motor operating at independent speeds of each other. The meter speed is determined by a combination of ground speed and desired population rate while the BrushBelt speed stays consistent with the forward ground speed of the planter in order to place the seed at the bottom of trench.
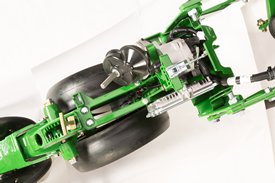

Industry-proven 56-V brushless motors give confidence to the operator that the row-unit will perform in any condition. The advantage of 56-V over 24-V electric motors is a lower amperage draw.
Brushless motors are maintenance free and give the producer the most optimal solution to achieve the highest performance and the lowest amount of work to the planter.
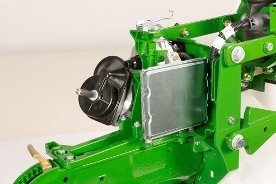

Manage seed output, reduce yield drag, and improve harvest capabilities are features built in to every ExactEmerge row-unit with electric motor shutoffs.
The electric drive version of RowCommand row-unit has the potential to get 2 to 8 percent reduction in seed usage from being able to control the meter and BrushBelt rather than a clutch disengaging and some seeds still falling down the seed tube.
SeedStar™ 4HP monitoring system – see speed meet accuracy in real time
Have you wanted to view more than one planter chart at once? SeedStar 4HP gives you multiple views and configurations in one simple overview page to fit your preferences. You can complete the simplified setup from the Work Setup page instead of having multiple applications to open.
SeedStar 4HP is designed to optimize the in-cab monitoring experience exclusively on the Gen 4 4600 CommandCenter™ display or 4640 Universal Display for growers with ExactEmerge™ planters and MaxEmerge™ 5e planters. With SeedStar 4HP, operators will easily see key planter information with customizable run pages, zoom functionality, and simultaneous graph and performance measurements. SeedStar 4HP is included in base on all model year 2018 ExactEmerge and MaxEmerge 5e planters.
Features overview:
- View multiple planters' at-a-glance bar charts simultaneously
- Three default planter run pages show key planter functions in easy-to-view layouts
- Highly configurable run pages allow SeedStar modules to be customizable
- Zoom feature allows quick row-by-row detailed information
- View dual bar graphs to see multiple planter details at one time
- SeedStar application to make adjustments to planter functions
- Simplified setup through the work set-up page
- Advanced rates allow up to six different rates across 48 rows
- The SeedStar 4HP monitoring system requires the Gen 4 4600 CommandCenter or 4640 Universal Display. These displays allow the operator to benefit from the updated interface, enhanced processing speeds, and easy setup (learn more here).
SeedStar 3 HP conversion to SeedStar 4HP with mobile row-unit runoff aftermarket for field conversion kits
Growers who are currently running model year 2017 planters, model year 2017 and newer performance upgrade kits, or model year 2017 and newer custom-built planters with the SeedStar 3 HP monitoring system can upgrade to the SeedStar 4HP monitoring system with mobile row-unit runoff. The attachment part, AA100382, is software only. The Gen 4 display software version will need to be 19-1 or newer and will require planter apps. Follow the mobile runoff ordering and software push guide below for ordering and installation. Retrofitted planters and custom-built planters will also require the John Deere Connect Mobile kit, 0048PC, from the Precision Ag Technology Price Pages and wiring harness AA83662 to enable the mobile row-unit runoff feature. Please reference Parts Advisor and CCMS Solution 105181 for model-specific mounting brackets. SeedStar 4HP requires the Gen 4 4600 CommandCenter v2 display or 4640 Universal Display.
Default planter run pages
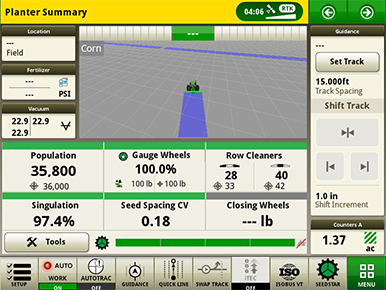
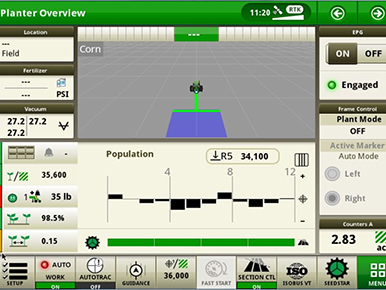
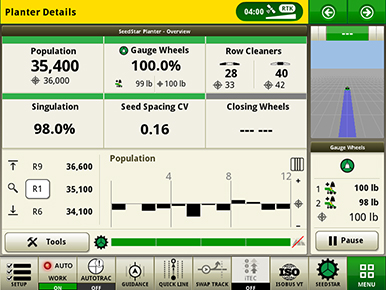
Three default run pages show key planter functions in different views to give fast and easy access to important planter information.
Custom run pages
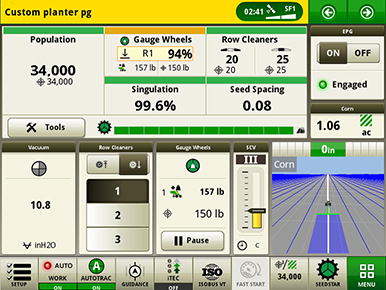
There are customizable run pages that allow the operator to build pages that fit their operation with different modules, like the example shown above.
Zoom functionality
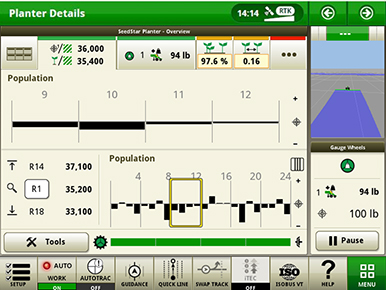
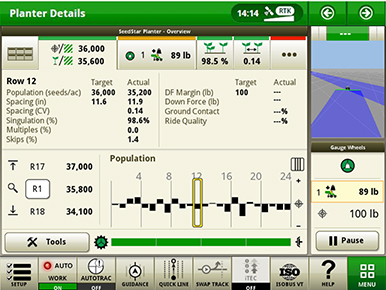
The zoom feature allows the operator to touch a section or row of the planter and get detailed information quickly.
Dual bar graphs
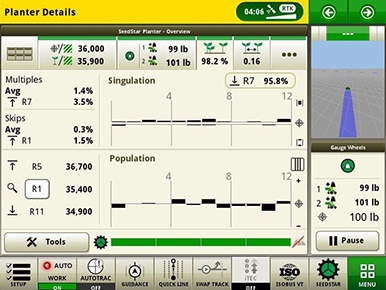
Dual bar graphs allow operators to view multiple planter details at one time.
SeedStar application page
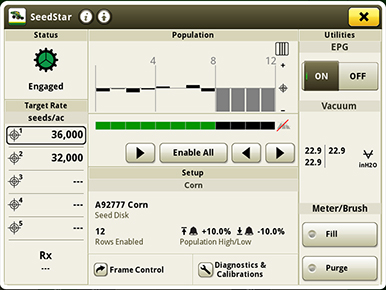
In the SeedStar application, many adjustments can be made, including manually activating section control. SeedStar 4HP allows up to 48 individual row sections. There are several setup features such as crop, seed disk, number of rows being planted, population alarms, and limits. Seed rates can be modified, electric power generation (EPG) can be turned on or off, vacuum can be adjusted, and the fill and purge functions can be used from the SeedStar application. Frame control, as well as diagnostics and calibrations, can be accessed at the bottom of the screen.
Settings Manager in SeedStar 4HP
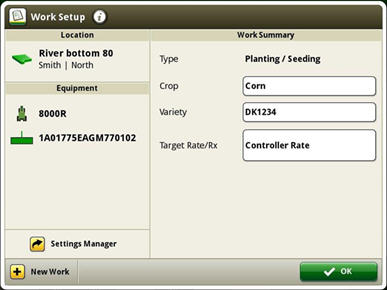
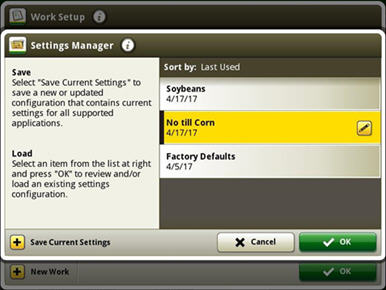
Reduce set-up time between changing crops or field conditions by recalling saved settings used previously with Settings Manager, included with every SeedStar 4HP system. This feature allows saving and recalling planter and tractor settings for optimum performance in different conditions.
Settings Manager can be used to save all the adjustment and inputs associated to a particular crop or condition. An example would be to store all population rates, downforce pressure, row cleaner adjustments, and closing wheel settings for planting corn and storing a separate, unique set of adjustments for soybeans. In addition, Settings Manager stores tractor settings such as selective control valve (SCV) flow and detents, infinitely variable transmission (IVT™) settings, eco modes, and more.
Compatibility
SeedStar 4HP compatibility | |
Planters | All models ordered with ExactEmerge or MaxEmerge 5e row-units NOTE: Performance upgrade kits are equipped with SeedStar 3HP only but can be upgraded by purchasing part number AA100382. |
Displays | Gen 4 4600 CommandCenter equipped with Version 2 Processor or 4640 Universal Display Dual-display mode is compatible with mid model year 2019 planter software. |
John Deere Active Implement Guidance™ | Compatible with SeedStar 4HP on Gen 4 displays with VT mode and required activations and subscriptions |
AutoTrac™ Implement Guidance | SeedStar 4HP is compatible with ATTA and ATIG; not compatible with >48 row electric drive planters. |
AutoTrac Turn Automation | SeedStar 4HP is compatible with ATTA and ATIG; not compatible with >48 row electric drive planters. |
Additional information
For additional information on feature functionality on the Gen 4 Display, visit the links below:
YouTube is a trademark of Google LLC.
Custom rates in SeedStar 4HP
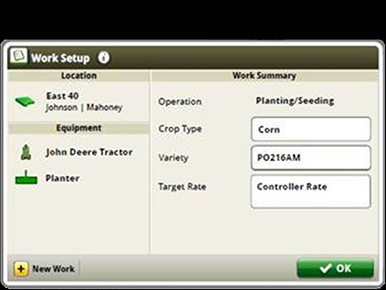
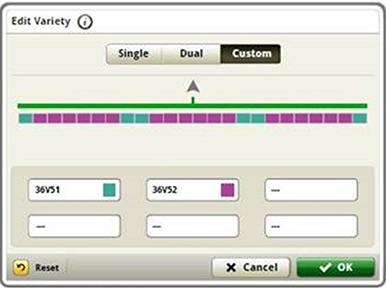
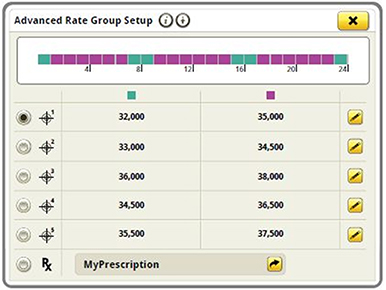
Custom rates allow for individual row population control and row-by-row documentation where up to six different rates can be assigned across an up to 48-row planter. This allows growers interested in planting seed corn with ExactEmerge or MaxEmerge 5e the capability to assign specific populations to male and female rows for planting. This feature can also be used to create tram lines or other applications where custom rates by row are needed.
NOTE: Individual rates are tied to varieties, so each individual rate needs a unique variety name.
NOTE: Advanced rates are not compatible with prescriptions or they cannot be run at the same time.
Increase productivity with ExactEmerge™ trench delivery system and BrushBelt™ delivery system
It is very challenging to get the crop planted during the optimum planting window or as close to the optimum planting day as possible. Rate-of-yield loss accelerates greatly after the optimum window has passed. This is especially true in the northern U.S. and Canada. ExactEmerge maintains accurate speed placement at higher speeds; growers can avoid missing that peak planting time, thereby helping to get the highest crop yields.
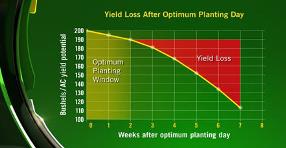

With the BrushBelt trench delivery system, the spacing in the trench does not change from even to uneven terrain. This can be a problem with a traditional seed tubes. Seed bounce and ricochet may occur as slopes increases, ultimately decreasing seed spacing performance.
The design of the BrushBelt system provides the best solution for the lowest release of seed to the bottom of the trench. The use of a brush provides the meter with an infinite amount of placement opportunities for each seed. This is what gives producers the confidence that every seed will have the desired spacing that a seed tube cannot provide.
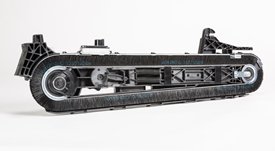

When the brush comes around the pulley, it expands and allows the seed to be transferred from the bowl to the brush very easily. The brush then carries the seed down toward the trench, ensuring that there is no movement as it moves down the length of the cartridge.
Once the brush reaches the lower pulley, the BrushBelt system expands again to loosen the grip on the seed, and the centrifugal force releases the seed. Another advantage with the BrushBelt system and cartridge at all speeds up to 10 mph is the ability to match the seed rearward trajectory to the forward ground speed of the planter. This provides a dead drop of the seed with no bounce and no roll at the bottom of the trench.
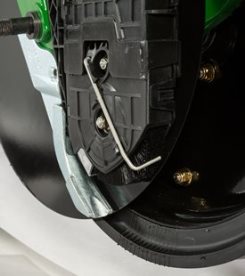

John Deere’s ExactEmerge cartridge is self-cleaning. When an operator uses seed treatments or is forced to plant in less than ideal soil conditions, the design of the trench delivery system sheds buildup from the BrushBelt. A brush conditioner is located at the bottom of the cartridge to remove remaining residue and prevent the bristles from sticking together.
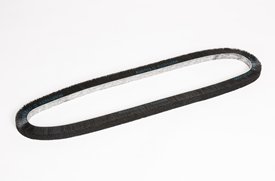

The BrushBelt system requires no maintenance and has a wear life designed to match the wear life of the other wear components. Since operations vary, as do soils and field content, it is recommended to replace the BrushBelt after noticeable wear or decreased performance.
Changing the belt is easy. One latch removes the meter over the trench delivery system. Grab the cartridge by the grip and pull toward the body, releasing it from the electric motor fitting. Lift the trench delivery system up and remove the sensor wiring harness to completely pull the cartridge out of the row-unit.
There are two plastic covers that snap off to uncover the belt; remove the covers and then twist the circular spring-tensioner dial with the yellow arrow on it to release the tension on the springs. Once tension has been removed, pull the belt out. It is also recommended to change the stainless-steel wear strip at this time as well, which also slides right out of place without the use of tools.
NOTE: It is recommended to use a talc/graphite mixture with ExactEmerge. Best results have been 80 percent talc and 20 percent graphite. For certain regions and territories, talc and talc/graphite mixes are restricted from use; in this case, use a wax-based fluency agent.
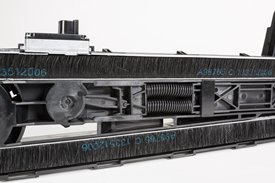

Another advantage over a seed tube is that the BrushBelt system also acts as a cleaner to the seed sensor compared to a seed tube.
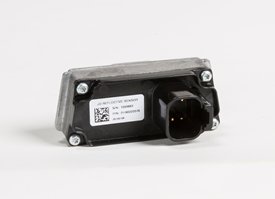
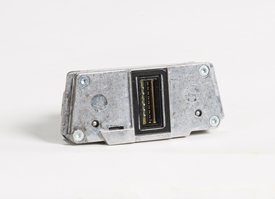
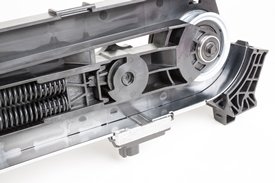
On all ExactEmerge row-units, each cartridge will be equipped with sensors. As the seeds are being delivered through the BrushBelt™ delivery system controls, they pass the reflective seed sensor. The delivery system slides every seed past the seed sensor to read and send the signal to the controller. The seed sensor and design is able to provide sensor performance at higher seeds per second with no population adjustment as needed with seed tube sensors. This seed sensor data is actual row-unit performance data. In comparison, seed tube sensors add 10 percent population in soybean planting to adjust for the seeds missed due to placement within the seed tube. The BrushBelt system holds each seed in place until released in the trench, allowing the seed sensor a more accurate read.
Downforce system options
Individual Row Hydraulic Downforce (IRHD)
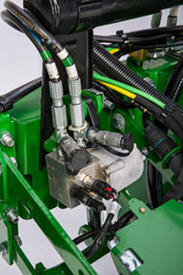
IRHD has been specifically designed to meet the needs of producers that are looking to adjust to the toughest field conditions and provide maximum yield potential from field to field, season after season. IRHD works as a closed-loop downforce system that reacts quickly on an individual row basis to changing soil conditions supporting increased ground contact, which can lead to improved seed depth consistency. When setting planter downforce margin, the system will apply the needed downforce by row to maintain ground contact. From the factory, the margin will be set at 45.4 kg (100 lb), changes may be required based on varying field conditions.
The system allows operators to maintain gauge wheel ground contact leading to desired seed depth placement. IRHD can adjust five times per second and make adjustments of 45.4 kg (100 lb) in less than a second. The system has a total range of applied downforce from 22.7 kg (50 lb) to 204.1 kg (450 lb) and utilizes the power beyond circuit on the tractor. IRHD is 58 percent faster than the active pneumatic downforce solution. Fast reaction and increased ground contact can lead to improved emergence. With uniform emergence, some studies have shown a yield impact from 5 percent to 9 percent.
IRHD is controlled through the display with SeedStar™ 3 HP or SeedStar 4HP. As shown below, operators can view ground contact or applied downforce using the toggle button.
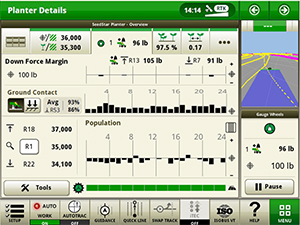
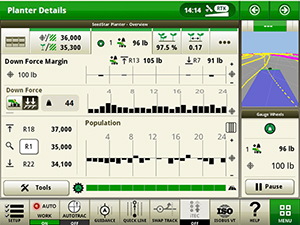
Hydraulically driven compressor
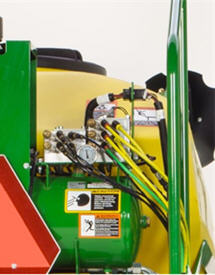
The hydraulically driven air compressor can deliver up to eight times the air flow when compared to the electric compressor, allowing for more and faster downforce changes to be made. This more robust design features a 37.8-L (10-gal.) storage tank across all models with active downforce.
At approximately 15.1 L/min (4 gpm), hydraulic demands are low and ties into the machine’s lift and Central Commodity System (CCS™) hydraulic circuit so it does not require any additional selective control valves (SCVs). The SeedStar XP, SeedStar 3 HP, and SeedStar 4 HP monitoring systems work with the compressor. SeedStar 3 HP and SeedStar 4 HP monitoring systems work with the compressor and valve assembly to regulate air to downforce springs, enabling the active control, pneumatic closing wheels, and pneumatic row cleaners.
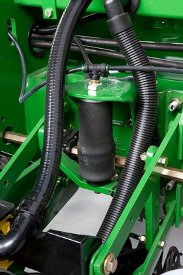
Each row-unit has a single rubber air bag located between the parallel arms. The air bags are hooked in parallel so that air can be added or released from all rows at once from one location.
The individual pneumatic downforce air bag assemblies, air compressor units, and 9.5-mm (3/8-in.) delivery lines are also available as an attachment for field conversion.
Row-unit downforce planter run page
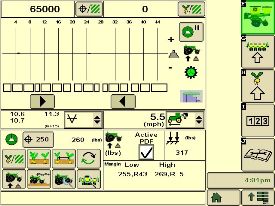
Active downforce control is integrated into SeedStar XP, SeedStar 3 HP, and SeedStar 4 HP monitoring systems.
Margin is the amount of weight riding on the depth gauge wheels that ensures desired firming of the seedbed as set by the operator.
Once a target margin has been defined, enter the value into the display and let active downforce do the rest. The system will actively adjust the air pressure in the air bags to maintain a constant margin across the planter. The changes in air pressure will change the amount of downforce placed on the row-unit, compensating and reacting for varying conditions through the field whether it is different tillage practices, soil types, or moisture.
Set point row-unit downforce
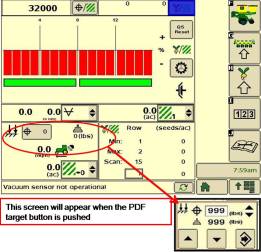
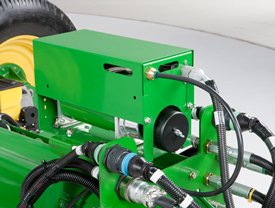
On set point, the air compressor will be mounted on the outer hitch or frame assembly. Since the electric air compressor assembly is mounted on the outer hitch (as noted in the picture above) or frame, adjustments for row-unit downforce and related system pressures will be made electronically with the GreenStar display.
When adjusting the amount of row-unit downforce using the GreenStar display, the operator will select the amount of downforce (kg [lb]) to be applied across the planter. Depending on the soil conditions at hand, the operator might need to adjust the relative amount of row-unit downforce being applied during the planting operation. The integrated pneumatic downforce controls within the GreenStar display will only allow for set-point operation and not automatic control as the planter is operating in different soil conditions. The pneumatic downforce system does not have the capability to automatically adjust downforce.
Pneumatic downforce provides convenient, simple adjustment of downforce for the whole planter from one location. The amount of downforce applied is infinitely adjustable from 6.8 to 181.4 kg (15 to 400 lb). Pneumatic downforce provides more consistent downforce throughout the range of row-unit travel than mechanical spring downforce systems.
Features include:
- 9.5-mm (3/8-in.) air delivery line instead of the 6.4-mm (1/4-in.) line used on model year 2010 and older planters.
- Air compressor assembly increased duty cycle. With this compressor, it provides a 47 percent increase in maximum air flow delivery compared to the prior air compressor.
- Pneumatic air bags with 9.5-mm (3/8-in.) air line inlets that have greater durability.
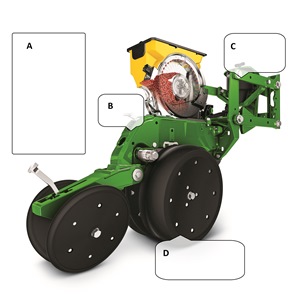
- A - Margin – amount of additional downforce applied to a row-unit above and beyond what is required for penetration to achieve planting depth. This additional weight will ride on the depth gauge wheels.
- 54.4 kg (120 lb) + 36.3 kg (80 lb) = 90.7 kg (200 lb) – 68 kg (150 lb) = 22.7 kg (50 lb) of margin
- B - Weight of row-unit - 54.4 kg (120 lb)
- C - Downforce – force that is applied to the row-unit by the air bag circuit - 36.3 kg (80 lb)
- D - Resistance from soil - 68 kg (150 lb)
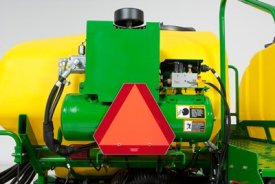
A hydraulically driven compressor works with the SeedStar XP, SeedStar 3 HP, and SeedStar 4 systems to automate downforce control. Just set the row-unit target margin value and the active pneumatic downforce system works automatically. The system will make sure the planter maintains this value, achieving precise soil penetration, and consistent planting depth, without sidewall soil compaction. From the factory, the system is set at 45.4 kg (100 lb) target downforce margin but may be modified for varying field conditions. This frees the operator from constantly making manual downforce adjustments as conditions change.
This system offers a split-rank control feature for 1795 and DB Split-Row Planters. On split-row planters, active downforce will control the front and rear rows independently. This compensates for differing downforce requirements between the ranks that can be caused by things like different tillage or insecticide attachments and will help maintain an accurate planting depth and consistent margin across all the rows.
Active pneumatic downforce is available as factory installed or as an attachment for field conversion.
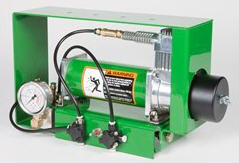
An improved compressor is used to charge the pneumatic system. This compressor can be located on the planter frame or in the tractor cab if desired. A gauge at the compressor indicates the amount of downforce being applied.
Integrated pneumatic downforce system
The functional features of the integrated system are the same as the standard pneumatic system, explained above, with the addition of control through the GreenStar display.
Heavy-duty adjustable downforce springs
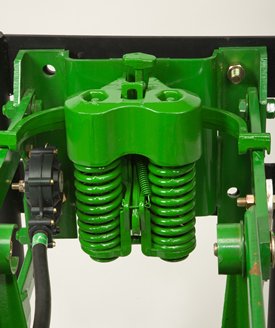
Planter row-unit downforce is an important factor to ensure consistent and proper depth control. The heavy-duty adjustable downforce feature provides up to 181.4 kg (400 lb) of downforce. There are four settings available to allow the operator to choose the amount of downforce required for the condition: 0 kg (0 lb), 56.7 kg (125 lb), 113.4 kg (250 lb), and 181.4 kg (400 lb).
Increase job performance when planting and spraying
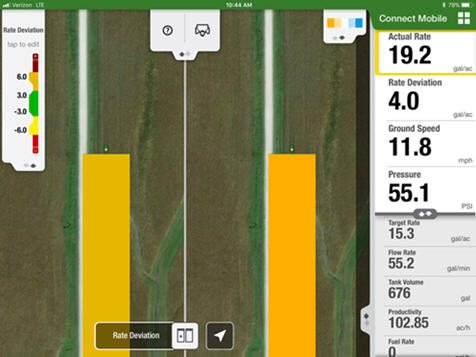
Connect Mobile overview
John Deere Connect Mobile is a solution that utilizes an Apple® iPad® tablet in the cab and helps the operator increase job performance during planting and spraying operations. Connect Mobile documents and displays multiple quality layers, helping the operator monitor and more easily detect problems that can occur during planting and spraying. Connect Mobile also has a common user interface that makes it easy to use between different pieces of John Deere equipment.
Planting attributes
Monitor and document key performance indicators in high-definition map layers and dashboard tiles such as:
- Actual population
- Target population
- Singulation
- Seed-spacing CV
- Applied downforce
- Gauge wheel margin
- Ride quality
- Ground speed
- Variety
Spraying attributes
- Actual rate
- Rate deviation
- Ground speed
- Pressure
In base equipment
Planting
Connect Mobile hardware is factory installed on all model year 2015 and newer planters factory installed with ExactEmerge™ row-units and all model year 2017 and newer planters factory installed with MaxEmerge™ 5e row-units, making it easy to get started with Connect Mobile.
Spraying
Connect Mobile hardware is factory installed on all model year 2018 Sprayers with the 4600 CommandCenter™ display. Producers can also retrofit Connect Mobile on older sprayers with a GreenStar™ 3 2630 Display by installing the sprayer field kit.
Learn more about Connect Mobile in the Field and Crop Solutions section within the Precision Ag Technology product line and how it can improve the quality of a planting and spraying job.
iPad and Apple are trademarks of Apple Inc.
Mobile row-unit runoff
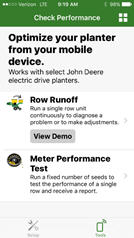
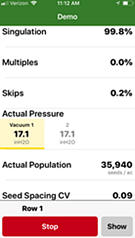
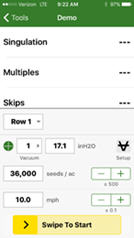
The first day of planting season can be as productive as the last with mobile row-unit runoff. The mobile row-unit runoff activation on the planter main controller (PMC) allows operators to make adjustments to maximize row-unit performance from a mobile device at the rear of the planter for both preseason and in-season use - all enabled through the PlanterPlus™ app.
Mobile row-unit runoff allows growers to perform test-stand functions from a mobile device connected to the planter.
The row runoff test provides complete diagnostic checks both preseason and in season. With the row-unit runoff test, the operator can make adjustments from the mobile device, including vacuum pressure, to determine the optimum meter and vacuum settings. This app functionality will help avoid making trips to the cab while validating meter performance.
During preseason planter inspections and set up, utilize the meter performance test to validate meter accuracy, similar to a test stand without leaving the farm. Test all systems on the planter, not just the meter, providing confidence that all planter systems are ready to plant. Reports are generated from the test providing information the operator can save and send for future reference.
Before heading to the field, the operator will benefit from knowing the best row-unit and vacuum settings for each variety selected to plant that spring.
Watch this video to see mobile row-unit runoff in action.
Mobile row-unit runoff will work with any model year 2015 or newer ExactEmerge™ or MaxEmerge™ 5e equipped planter. Mobile row-unit runoff can be added with attachment AA93169.
For model year 2018 and newer ExactEmerge planters, mobile row-unit runoff is included in base equipment. For model year 2020 and newer MaxEmerge 5e planters, mobile row-unit runoff is included in base equipment. For planters not equipped from the factory, mobile row-unit runoff can be added with attachment AA93169. A mobile row-unit runoff and Easy Fold package can be added with attachment AA97849 (only available with 1775NT and 1795 Planters with a 2-point hitch and model year 2019 and newer DB Planters with Gen 4 based frame folding).
NOTE: Mobile runoff utilizes PlanterPlus app available on select iPad® tablets, iPhone® smartphones, and Android™ devices.
Mobile row-unit runoff and Easy Fold aftermarket for field conversion kits
The below software bundles include the functionality explained above for machines not ordered with the feature from the factory. Compatible machines include all the necessary sensors and harnesses needed to make the feature function. The attachment part is software only. Follow the mobile runoff ordering and software push guide below for ordering and installation.
SeedStar™ 3 HP conversion to SeedStar 4HP
Mobile runoff ordering and software push guide
iPad and iPhone are trademarks of Apple Inc. Android is a trademark of Google LLC.
John Deere Connected Support™ prevents downtime and efficiently resolves issues with revolutionary technology-based solutions
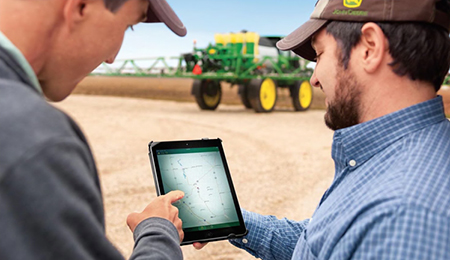
When you buy John Deere equipment, you expect reliability. You also know that problems can happen, and a product is only as good as the support behind it. That’s why John Deere equipment is prepared with technology that senses potential issues and can alert you and your dealer promptly—in the cab or anywhere you are.
John Deere Connected Support is a revolutionary change to support that leverages technology and the connectivity of JDLink™ telematics to prevent downtime and resolve problems faster. These tools decrease downtime by an average of 20 percent, enabling faster responses to unexpected problems and reducing technician trips to your machine. For some issues, unplanned downtime can even be prevented altogether through prediction of the issue.
With your permission, John Deere Connected Support:
- Keeps you running by monitoring machine health and promptly alerting you and your dealer of issues
- Saves time by remotely viewing in-cab displays, reducing trips to the machine
- Reduces or even eliminates technician trips to a machine through remote diagnostic and remote software reprogramming capabilities
- Connects experts with the information needed to respond to downtime faster and prevent it altogether
With more than a decade of experience leveraging connectivity to solve problems, no one else has the experience, tools, and knowledge to keep you running as John Deere and your John Deere dealer can. Connected Support is an in-base feature on all John Deere products with factory- or field-installed JDLink.
Pneumatic closing wheels
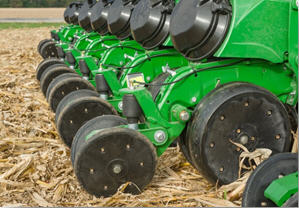
Pneumatic closing wheels are compatible with MaxEmerge™ 5e and ExactEmerge™ row-units. They are available on the following models from the factory: 1775NT, 1795, and DB60 models. The pneumatic closing wheels give operators the ability to adjust closing wheels in seconds without leaving the cab of the tractor.
Using the GreenStar™ 3 2630 Display, pneumatic closing wheels can be adjusted to 25 different positions. From the factory the system is setup with two sections, the outer wings and center frame. With this system, producers will see up to a 76 percent increase in consistent force applied at the closing wheel. Consistently applying the correct force at the seed trench is one of the key elements of supporting improved emergence. Studies show potential yield impact on corn from even emergence from 5 percent to 9 percent*.
NOTE: Pneumatic closing wheels can be purchased for existing MaxEmerge 5e and ExactEmerge planters as an aftermarket field kit. Both rubber tire and cast-iron closing wheels are compatible.
Refer to the operator’s manual for guidance on settings, including when upgrading from springs to pneumatic.
Access the pneumatic closing wheels attachment for field conversion (AFC) ordering guide to fit a 1725 CCS, 1775NT, 1795, or DB60 Planter.
*Source: Planting Outcome Effects on Corn Yield: Doerge, Tom, Jeschke, Mark and Carter, Paul
Specifications
- Additional Information - Recommended tractor horsepower: Minimum required for 9.1 m (30 ft) models: 201 kW<br/>270 hp<br/>Minimum required for 12.2 m (40 ft) models: 268 kW<br/>360 hp
- Additional Information - Recommended tractor hydraulics: Hydraulic oil pump required to operate ExactEmerge™ planter: 227 L/min<br/>60 gpm<br/>Tractor standby pressure: 15,500 kPa<br/>155 bar (2300 psi)<br/>Hydraulic system working pressure: 20,684 kPa<br/>207 bar (3000 psi)<br/>Hydraulic system burst pressure: 82,737 kPa<br/>827 bar (12,000 psi)
- Closing System - Cast iron closing system: <br/><br/>
- Closing System - Rubber tire closing system: <br/><br/><br/>
- Dimensions - Field operation length: 31R15 and 32R15: 7.7 m<br/>25.34 ft
- Dimensions - Field operation width: 31R15 and 32R15: 13.0 m<br/>42.81 ft
- Dimensions - Transport height: 31R15 and 32R15: 3.96 m<br/>13 ft
- Dimensions - Transport length: 31R15 and 32R15: 10.46 m<br/>34.33 ft
- Dimensions - Transport width (with markers): 31R15 and 32R15: 4.01 m<br/>13.17 ft
- Drive System - Base: 56 V Electric motors
- Fertilizer - Dry fertilizer: <br/>
- Fertilizer - Fertilizer opener type: <br/>
- Frame - Flexibility: Up and down: 15 degree (angle)
- Key Specs - Frame - Flexibility: Up and down: 15 degree (angle)
- Key Specs - Number of rows: 31 or 32
- Key Specs - Row spacing: 31R15 and 32R15: 38 cm<br/>15 in.
- Key Specs - Row unit seed hoppers: Capacity<br/>Vacuum meter: 2.2 L<br/>0.62 bu<br/>
- Key Specs - Seed Meters: Base<br/>Vacuum<br/><br/>
- Lift System - Type: Wheel modules with rephasing hydraulic cylinders
- Markers - Control: <br/>
- Markers - Marker disk: <br/>
- Markers - Type: Automatic alternating or independent control
- Row Units - Opener: Tru-Vee Double Disk
- Row Units - Row unit down force: <br/><br/>
- Row Units - Row unit seed hoppers: Capacity<br/>Vacuum meter: 2.2 L<br/>0.063 bu<br/>
- Row Units - Scrapers, opener blades: <br/><br/>
- Row Units - Seed tube sensors: <br/>
- Row Units - Type: Standard: MaxEmerge™ 5 row units<br/>Optional: ExactEmerge™ row units<br/>MaxEmerge 5e row units
- Rows and Row Spacing - Number of rows: 31 or 32
- Rows and Row Spacing - Row spacing: 31R15 and 32R15: 38 cm<br/>15 in.
- Seed Meters - Base: Vacuum
- Seed Meters - Central Commodity System: Seed capacity<br/>2467 L<br/>70 bu<br/>3524 L<br/>100 bu<br/>
- Seed Monitor System - Base: SeedStar™ on GreenStar™ displays
- Tires - Base: Fertilizer contact drive tire: 18x9.56-8 4PR: 193 kPa<br/>1.93 bar (28 psi)<br/>Center grame tires (4 per machine): 31R15,32R15, 24R20, 23R15and 24R15 with fertilizer: 11R22.5 TL LR F: 414 kPa<br/>4.14 bar (60 psi)<br/>Wing tires (4 per machine): 10x15 LR D: 279 kPa<br/>2.758 bar (40 psi)
Features
- Central Commodity System (CCS): 100 bushels; 130 bushels
- Number of Rows: 16/31 or 16/32
- Row Unit: ExactEmerge, MaxEmerge 5e, MaxEmerge 5
- Spacing (inches): 30/15
- Transport Width: 12 ft., 12 ft. 11 in.
Copy Set
Precise liquid fertilizer placement with ExactRate™ fertilizer system
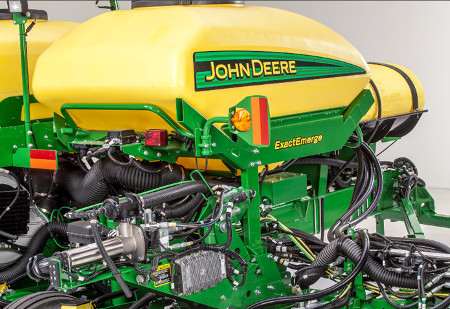
The ExactRate liquid fertilizer system is a factory-installed solution that provides you with accurate nutrient placement during planting. Previously, you would have to deal with the inconvenience of cumbersome aftermarket systems for a hydraulically driven variable-rate solution. With ExactRate, John Deere delivers a complete planting solution for liquid fertilizer users. You can choose between in-furrow or offset delivery methods. This system delivers:
- Up to 20 percent more accurate nutrient placement in a turn compared to a non-turn compensating systems
- 1 to 12 percent (4.3 percent on average) reduction in inputs through row-by-row section control
- Ability to run up to 16.1 km/h (10 mph)
- Closed-loop speed and rate change compensation
- Full integration into the 4600 CommandCenter™ and 4640 Universal Display
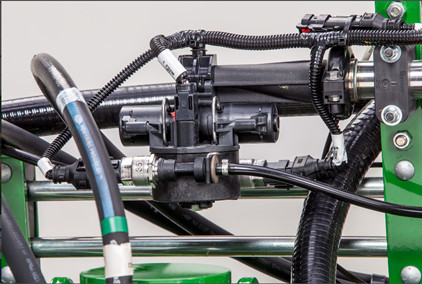
The ExactRate liquid fertilizer system is designed to take full advantage of the capabilities of ExactEmerge™ and MaxEmerge™ 5e planters. This factory-installed liquid fertilizer system delivers the same value as your electric drive planter including working at speeds faster than the traditional 8.05 km/h (5 mph), turn compensation, and row-by-row section control, all while accurately compensating for varying rates and speed changes. Additional features include row-by-row flow detection, as-applied documentation, and variable-rate capabilities, providing operators full integration into the 4600 CommandCenter or 4640 Universal Display.
Fertilizer flows from the tank to the pump, through a strainer and boom isolation valve, through a central flowmeter, and out to each nozzle body and row-unit for accurate delivery. The system is closed loop, meaning the pump and nozzle body duty cycle both adjust based on feedback received from the pressure sensor and central flowmeter. This design helps maintain an accurate application rate.
NOTE: ExactRate is not recommended for products that require agitation to maintain suspension.
Pump
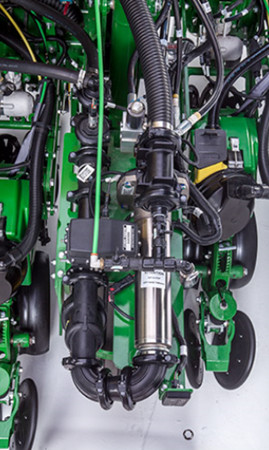
Instead of a tire-contact drive, a hydraulically driven centrifugal pump eliminates chain and sprocket adjustments to provide more speed flexibility over the entire rate range. This pump allows for a wide range of rate capabilities as well as strong durability. The wet seal design helps protect the pump if it is accidentally run dry for a short time.
Strainer
A strainer helps collect suspended particles and prevent them from causing blockages in the distribution system and nozzle bodies.
Boom isolation valve
The valve prevents the tank from draining out if there is a leak in the distribution system. If the pump is on, the valve opens to allow flow. When the pump is off, the valve closes.
Central flowmeter and pump pressure sensor
The central flowmeter and pump pressure sensor provide the rate control system feedback on flow and pressure to ensure an accurate application rate across the entire planter width. The flowmeter also supplies the as-applied rate data.
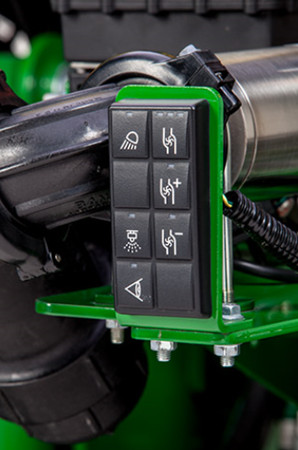
Just like on the sprayers, the keypad at the rear of the machine lets you conveniently perform a nozzle flow check to ensure product is coming out of each row before going to the field.
Direct injection
The ExactRate liquid fertilizer system does not have direct injection capabilities on the product being applied. If direct injection is needed on the secondary product, an additional rate controller is required.
NOTE: ExactRate system and John Deere Rate Controller 2000 with Raven ICD Direct Injection system is supported. ExactRate system and GreenStar Rate Controller with Raven ISO Direct Injection system is not supported.
Distribution system and nozzle body
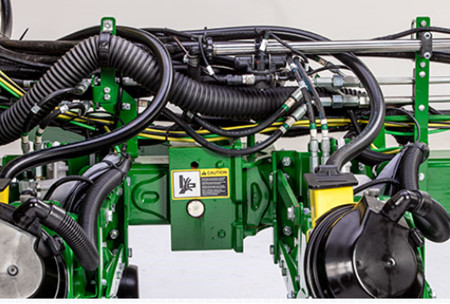
The 2.5-cm (1-in.) stainless-steel distribution lines not only reduce corrosion, they also provide a clean integrated look. The distribution system is pressure tested at the factory to reduce the risk of leaks.
John Deere has leveraged ExactApply™ technology and capabilities from the sprayers to enable row-by-row section control and turn compensation that matches the high-performance planters. With ExactRate, there are no orifice changes for rate or speed adjustments, saving you time and effort while limiting exposure to product. Pulse-width modulation technology varies duty cycle (opening and closing of the valve) in the nozzle bodies in conjunction with flow and pressure measured from central flowmeter and pressure sensor controlling the system pump. The ExactRate liquid fertilizer system uses one nozzle body for two rows, limiting the number of parts and complexity on each machine. While you’re in the cab, you’ll be able to keep an eye on each row with flow detection integrated into the Gen 4 display. The system will warn you if it detects a variance in an individual row’s flow. A pressure sensor integrated into the nozzle body will detect a flow reduction or overapplication on the row.
Rate Controller
The ExactRate liquid fertilizer system is compatible with the John Deere Rate Controller 2000 and GreenStar™ Rate Controller if a producer wants to apply a second product using a separate distribution system.
ExactRate app on Gen 4
Easily adjust target rate and speed without leaving your seat. With turn compensation, inner and outer rates are automatically adjusted to maintain consistent application across the full width of the planter. This ultimately reduces the risk of seed burn by over application (turn compensations require a global positioning system [GPS] receiver). Another helpful feature is row-by-row section control for reduced overlap on headlands and waterways. Gen 4 Documentation creates as-applied maps showing what product was applied where, providing accurate record-keeping.
Dual 56-V electric motors for ExactEmerge™ row-units
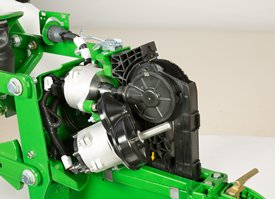
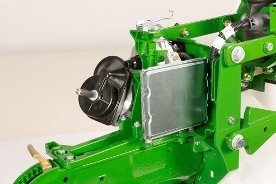
Two 56-V brushless electric motors provide ExactEmerge the upper hand over any other row-unit on the market. One motor controls the high-performance meter and the other powers the BrushBelt™ delivery system. Both feature a closed loop system ensuring they operate at the correct rpm.
The motor is controlled at a rate of 200 times per second and a decision is made every 5 milliseconds. The controller also keeps each motor operating at independent speeds of each other. The meter speed is determined by a combination of ground speed and desired population rate while the BrushBelt speed stays consistent with the forward ground speed of the planter in order to place the seed at the bottom of trench.
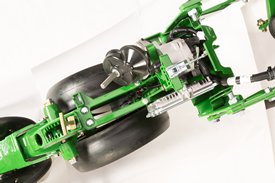

Industry-proven 56-V brushless motors give confidence to the operator that the row-unit will perform in any condition. The advantage of 56-V over 24-V electric motors is a lower amperage draw.
Brushless motors are maintenance free and give the producer the most optimal solution to achieve the highest performance and the lowest amount of work to the planter.
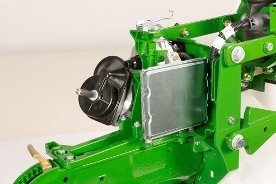

Manage seed output, reduce yield drag, and improve harvest capabilities are features built in to every ExactEmerge row-unit with electric motor shutoffs.
The electric drive version of RowCommand row-unit has the potential to get 2 to 8 percent reduction in seed usage from being able to control the meter and BrushBelt rather than a clutch disengaging and some seeds still falling down the seed tube.
SeedStar™ 4HP monitoring system – see speed meet accuracy in real time
Have you wanted to view more than one planter chart at once? SeedStar 4HP gives you multiple views and configurations in one simple overview page to fit your preferences. You can complete the simplified setup from the Work Setup page instead of having multiple applications to open.
SeedStar 4HP is designed to optimize the in-cab monitoring experience exclusively on the Gen 4 4600 CommandCenter™ display or 4640 Universal Display for growers with ExactEmerge™ planters and MaxEmerge™ 5e planters. With SeedStar 4HP, operators will easily see key planter information with customizable run pages, zoom functionality, and simultaneous graph and performance measurements. SeedStar 4HP is included in base on all model year 2018 ExactEmerge and MaxEmerge 5e planters.
Features overview:
- View multiple planters' at-a-glance bar charts simultaneously
- Three default planter run pages show key planter functions in easy-to-view layouts
- Highly configurable run pages allow SeedStar modules to be customizable
- Zoom feature allows quick row-by-row detailed information
- View dual bar graphs to see multiple planter details at one time
- SeedStar application to make adjustments to planter functions
- Simplified setup through the work set-up page
- Advanced rates allow up to six different rates across 48 rows
- The SeedStar 4HP monitoring system requires the Gen 4 4600 CommandCenter or 4640 Universal Display. These displays allow the operator to benefit from the updated interface, enhanced processing speeds, and easy setup (learn more here).
SeedStar 3 HP conversion to SeedStar 4HP with mobile row-unit runoff aftermarket for field conversion kits
Growers who are currently running model year 2017 planters, model year 2017 and newer performance upgrade kits, or model year 2017 and newer custom-built planters with the SeedStar 3 HP monitoring system can upgrade to the SeedStar 4HP monitoring system with mobile row-unit runoff. The attachment part, AA100382, is software only. The Gen 4 display software version will need to be 19-1 or newer and will require planter apps. Follow the mobile runoff ordering and software push guide below for ordering and installation. Retrofitted planters and custom-built planters will also require the John Deere Connect Mobile kit, 0048PC, from the Precision Ag Technology Price Pages and wiring harness AA83662 to enable the mobile row-unit runoff feature. Please reference Parts Advisor and CCMS Solution 105181 for model-specific mounting brackets. SeedStar 4HP requires the Gen 4 4600 CommandCenter v2 display or 4640 Universal Display.
Default planter run pages
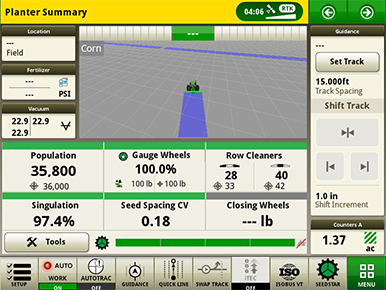
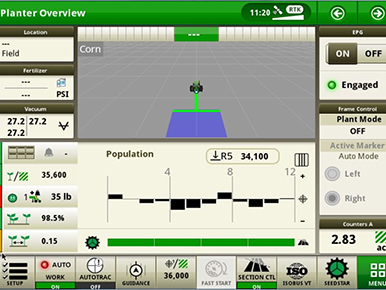
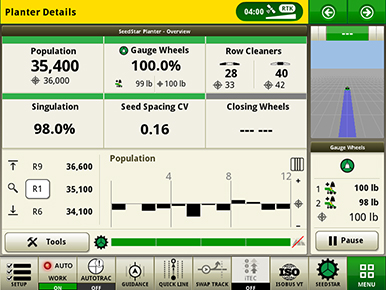
Three default run pages show key planter functions in different views to give fast and easy access to important planter information.
Custom run pages
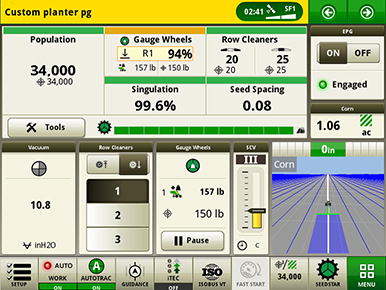
There are customizable run pages that allow the operator to build pages that fit their operation with different modules, like the example shown above.
Zoom functionality
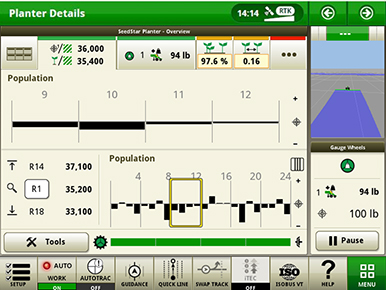
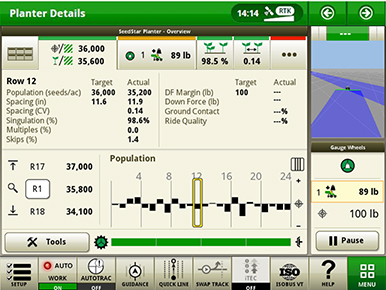
The zoom feature allows the operator to touch a section or row of the planter and get detailed information quickly.
Dual bar graphs
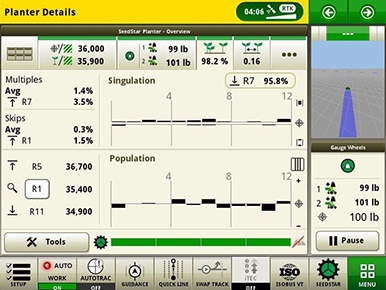
Dual bar graphs allow operators to view multiple planter details at one time.
SeedStar application page
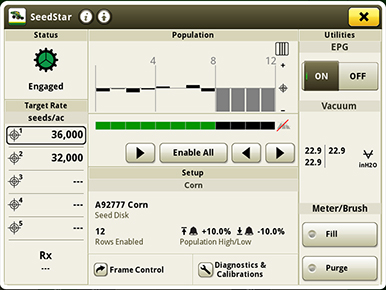
In the SeedStar application, many adjustments can be made, including manually activating section control. SeedStar 4HP allows up to 48 individual row sections. There are several setup features such as crop, seed disk, number of rows being planted, population alarms, and limits. Seed rates can be modified, electric power generation (EPG) can be turned on or off, vacuum can be adjusted, and the fill and purge functions can be used from the SeedStar application. Frame control, as well as diagnostics and calibrations, can be accessed at the bottom of the screen.
Settings Manager in SeedStar 4HP
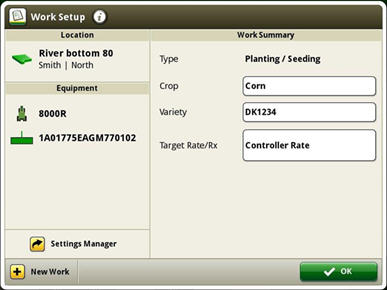
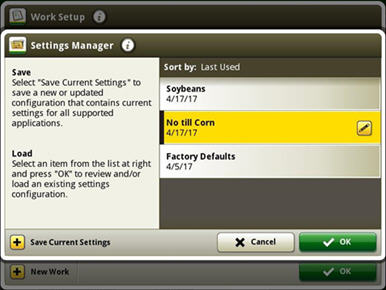
Reduce set-up time between changing crops or field conditions by recalling saved settings used previously with Settings Manager, included with every SeedStar 4HP system. This feature allows saving and recalling planter and tractor settings for optimum performance in different conditions.
Settings Manager can be used to save all the adjustment and inputs associated to a particular crop or condition. An example would be to store all population rates, downforce pressure, row cleaner adjustments, and closing wheel settings for planting corn and storing a separate, unique set of adjustments for soybeans. In addition, Settings Manager stores tractor settings such as selective control valve (SCV) flow and detents, infinitely variable transmission (IVT™) settings, eco modes, and more.
Compatibility
SeedStar 4HP compatibility | |
Planters | All models ordered with ExactEmerge or MaxEmerge 5e row-units NOTE: Performance upgrade kits are equipped with SeedStar 3HP only but can be upgraded by purchasing part number AA100382. |
Displays | Gen 4 4600 CommandCenter equipped with Version 2 Processor or 4640 Universal Display Dual-display mode is compatible with mid model year 2019 planter software. |
John Deere Active Implement Guidance™ | Compatible with SeedStar 4HP on Gen 4 displays with VT mode and required activations and subscriptions |
AutoTrac™ Implement Guidance | SeedStar 4HP is compatible with ATTA and ATIG; not compatible with >48 row electric drive planters. |
AutoTrac Turn Automation | SeedStar 4HP is compatible with ATTA and ATIG; not compatible with >48 row electric drive planters. |
Additional information
For additional information on feature functionality on the Gen 4 Display, visit the links below:
YouTube is a trademark of Google LLC.
Custom rates in SeedStar 4HP
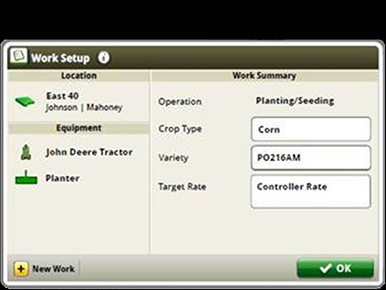
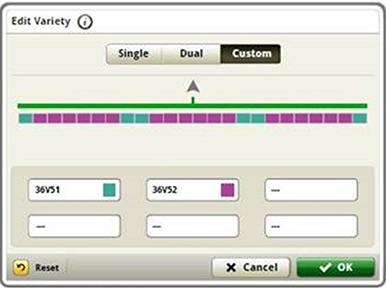
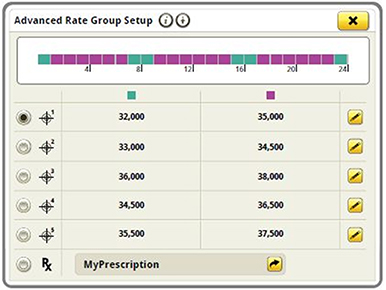
Custom rates allow for individual row population control and row-by-row documentation where up to six different rates can be assigned across an up to 48-row planter. This allows growers interested in planting seed corn with ExactEmerge or MaxEmerge 5e the capability to assign specific populations to male and female rows for planting. This feature can also be used to create tram lines or other applications where custom rates by row are needed.
NOTE: Individual rates are tied to varieties, so each individual rate needs a unique variety name.
NOTE: Advanced rates are not compatible with prescriptions or they cannot be run at the same time.
Increase productivity with ExactEmerge™ trench delivery system and BrushBelt™ delivery system
It is very challenging to get the crop planted during the optimum planting window or as close to the optimum planting day as possible. Rate-of-yield loss accelerates greatly after the optimum window has passed. This is especially true in the northern U.S. and Canada. ExactEmerge maintains accurate speed placement at higher speeds; growers can avoid missing that peak planting time, thereby helping to get the highest crop yields.
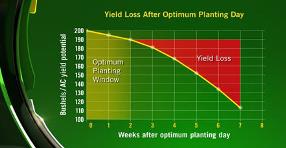

With the BrushBelt trench delivery system, the spacing in the trench does not change from even to uneven terrain. This can be a problem with a traditional seed tubes. Seed bounce and ricochet may occur as slopes increases, ultimately decreasing seed spacing performance.
The design of the BrushBelt system provides the best solution for the lowest release of seed to the bottom of the trench. The use of a brush provides the meter with an infinite amount of placement opportunities for each seed. This is what gives producers the confidence that every seed will have the desired spacing that a seed tube cannot provide.
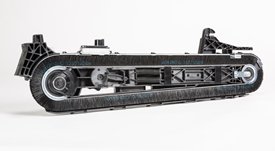

When the brush comes around the pulley, it expands and allows the seed to be transferred from the bowl to the brush very easily. The brush then carries the seed down toward the trench, ensuring that there is no movement as it moves down the length of the cartridge.
Once the brush reaches the lower pulley, the BrushBelt system expands again to loosen the grip on the seed, and the centrifugal force releases the seed. Another advantage with the BrushBelt system and cartridge at all speeds up to 10 mph is the ability to match the seed rearward trajectory to the forward ground speed of the planter. This provides a dead drop of the seed with no bounce and no roll at the bottom of the trench.
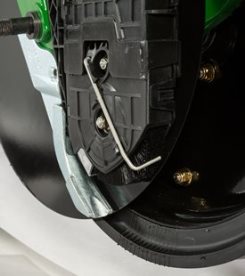

John Deere’s ExactEmerge cartridge is self-cleaning. When an operator uses seed treatments or is forced to plant in less than ideal soil conditions, the design of the trench delivery system sheds buildup from the BrushBelt. A brush conditioner is located at the bottom of the cartridge to remove remaining residue and prevent the bristles from sticking together.
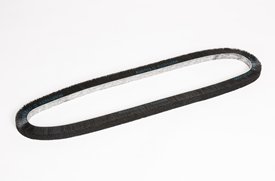

The BrushBelt system requires no maintenance and has a wear life designed to match the wear life of the other wear components. Since operations vary, as do soils and field content, it is recommended to replace the BrushBelt after noticeable wear or decreased performance.
Changing the belt is easy. One latch removes the meter over the trench delivery system. Grab the cartridge by the grip and pull toward the body, releasing it from the electric motor fitting. Lift the trench delivery system up and remove the sensor wiring harness to completely pull the cartridge out of the row-unit.
There are two plastic covers that snap off to uncover the belt; remove the covers and then twist the circular spring-tensioner dial with the yellow arrow on it to release the tension on the springs. Once tension has been removed, pull the belt out. It is also recommended to change the stainless-steel wear strip at this time as well, which also slides right out of place without the use of tools.
NOTE: It is recommended to use a talc/graphite mixture with ExactEmerge. Best results have been 80 percent talc and 20 percent graphite. For certain regions and territories, talc and talc/graphite mixes are restricted from use; in this case, use a wax-based fluency agent.
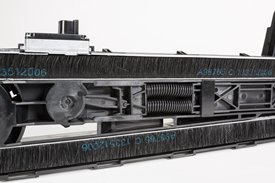

Another advantage over a seed tube is that the BrushBelt system also acts as a cleaner to the seed sensor compared to a seed tube.
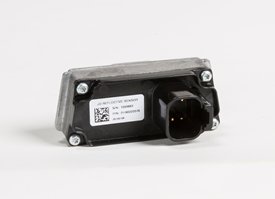
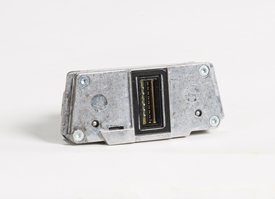
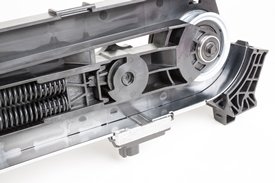
On all ExactEmerge row-units, each cartridge will be equipped with sensors. As the seeds are being delivered through the BrushBelt™ delivery system controls, they pass the reflective seed sensor. The delivery system slides every seed past the seed sensor to read and send the signal to the controller. The seed sensor and design is able to provide sensor performance at higher seeds per second with no population adjustment as needed with seed tube sensors. This seed sensor data is actual row-unit performance data. In comparison, seed tube sensors add 10 percent population in soybean planting to adjust for the seeds missed due to placement within the seed tube. The BrushBelt system holds each seed in place until released in the trench, allowing the seed sensor a more accurate read.
Downforce system options
Individual Row Hydraulic Downforce (IRHD)
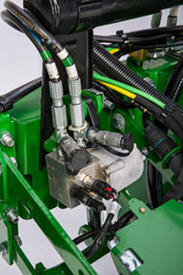
IRHD has been specifically designed to meet the needs of producers that are looking to adjust to the toughest field conditions and provide maximum yield potential from field to field, season after season. IRHD works as a closed-loop downforce system that reacts quickly on an individual row basis to changing soil conditions supporting increased ground contact, which can lead to improved seed depth consistency. When setting planter downforce margin, the system will apply the needed downforce by row to maintain ground contact. From the factory, the margin will be set at 45.4 kg (100 lb), changes may be required based on varying field conditions.
The system allows operators to maintain gauge wheel ground contact leading to desired seed depth placement. IRHD can adjust five times per second and make adjustments of 45.4 kg (100 lb) in less than a second. The system has a total range of applied downforce from 22.7 kg (50 lb) to 204.1 kg (450 lb) and utilizes the power beyond circuit on the tractor. IRHD is 58 percent faster than the active pneumatic downforce solution. Fast reaction and increased ground contact can lead to improved emergence. With uniform emergence, some studies have shown a yield impact from 5 percent to 9 percent.
IRHD is controlled through the display with SeedStar™ 3 HP or SeedStar 4HP. As shown below, operators can view ground contact or applied downforce using the toggle button.
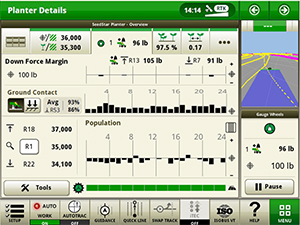
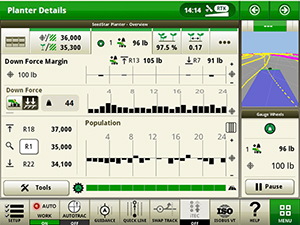
Hydraulically driven compressor
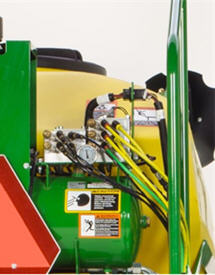
The hydraulically driven air compressor can deliver up to eight times the air flow when compared to the electric compressor, allowing for more and faster downforce changes to be made. This more robust design features a 37.8-L (10-gal.) storage tank across all models with active downforce.
At approximately 15.1 L/min (4 gpm), hydraulic demands are low and ties into the machine’s lift and Central Commodity System (CCS™) hydraulic circuit so it does not require any additional selective control valves (SCVs). The SeedStar XP, SeedStar 3 HP, and SeedStar 4 HP monitoring systems work with the compressor. SeedStar 3 HP and SeedStar 4 HP monitoring systems work with the compressor and valve assembly to regulate air to downforce springs, enabling the active control, pneumatic closing wheels, and pneumatic row cleaners.
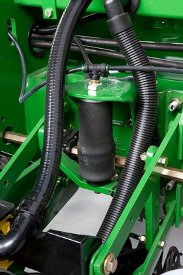
Each row-unit has a single rubber air bag located between the parallel arms. The air bags are hooked in parallel so that air can be added or released from all rows at once from one location.
The individual pneumatic downforce air bag assemblies, air compressor units, and 9.5-mm (3/8-in.) delivery lines are also available as an attachment for field conversion.
Row-unit downforce planter run page
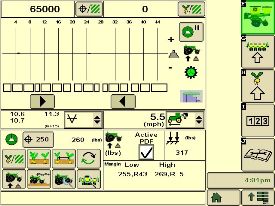
Active downforce control is integrated into SeedStar XP, SeedStar 3 HP, and SeedStar 4 HP monitoring systems.
Margin is the amount of weight riding on the depth gauge wheels that ensures desired firming of the seedbed as set by the operator.
Once a target margin has been defined, enter the value into the display and let active downforce do the rest. The system will actively adjust the air pressure in the air bags to maintain a constant margin across the planter. The changes in air pressure will change the amount of downforce placed on the row-unit, compensating and reacting for varying conditions through the field whether it is different tillage practices, soil types, or moisture.
Set point row-unit downforce
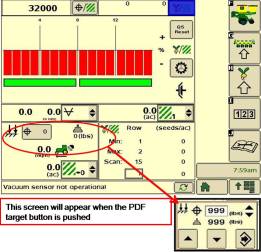
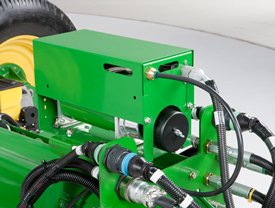
On set point, the air compressor will be mounted on the outer hitch or frame assembly. Since the electric air compressor assembly is mounted on the outer hitch (as noted in the picture above) or frame, adjustments for row-unit downforce and related system pressures will be made electronically with the GreenStar display.
When adjusting the amount of row-unit downforce using the GreenStar display, the operator will select the amount of downforce (kg [lb]) to be applied across the planter. Depending on the soil conditions at hand, the operator might need to adjust the relative amount of row-unit downforce being applied during the planting operation. The integrated pneumatic downforce controls within the GreenStar display will only allow for set-point operation and not automatic control as the planter is operating in different soil conditions. The pneumatic downforce system does not have the capability to automatically adjust downforce.
Pneumatic downforce provides convenient, simple adjustment of downforce for the whole planter from one location. The amount of downforce applied is infinitely adjustable from 6.8 to 181.4 kg (15 to 400 lb). Pneumatic downforce provides more consistent downforce throughout the range of row-unit travel than mechanical spring downforce systems.
Features include:
- 9.5-mm (3/8-in.) air delivery line instead of the 6.4-mm (1/4-in.) line used on model year 2010 and older planters.
- Air compressor assembly increased duty cycle. With this compressor, it provides a 47 percent increase in maximum air flow delivery compared to the prior air compressor.
- Pneumatic air bags with 9.5-mm (3/8-in.) air line inlets that have greater durability.
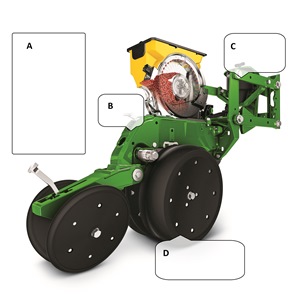
- A - Margin – amount of additional downforce applied to a row-unit above and beyond what is required for penetration to achieve planting depth. This additional weight will ride on the depth gauge wheels.
- 54.4 kg (120 lb) + 36.3 kg (80 lb) = 90.7 kg (200 lb) – 68 kg (150 lb) = 22.7 kg (50 lb) of margin
- B - Weight of row-unit - 54.4 kg (120 lb)
- C - Downforce – force that is applied to the row-unit by the air bag circuit - 36.3 kg (80 lb)
- D - Resistance from soil - 68 kg (150 lb)
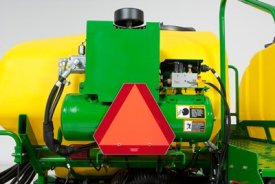
A hydraulically driven compressor works with the SeedStar XP, SeedStar 3 HP, and SeedStar 4 systems to automate downforce control. Just set the row-unit target margin value and the active pneumatic downforce system works automatically. The system will make sure the planter maintains this value, achieving precise soil penetration, and consistent planting depth, without sidewall soil compaction. From the factory, the system is set at 45.4 kg (100 lb) target downforce margin but may be modified for varying field conditions. This frees the operator from constantly making manual downforce adjustments as conditions change.
This system offers a split-rank control feature for 1795 and DB Split-Row Planters. On split-row planters, active downforce will control the front and rear rows independently. This compensates for differing downforce requirements between the ranks that can be caused by things like different tillage or insecticide attachments and will help maintain an accurate planting depth and consistent margin across all the rows.
Active pneumatic downforce is available as factory installed or as an attachment for field conversion.
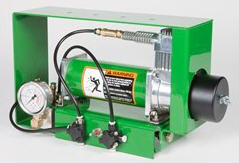
An improved compressor is used to charge the pneumatic system. This compressor can be located on the planter frame or in the tractor cab if desired. A gauge at the compressor indicates the amount of downforce being applied.
Integrated pneumatic downforce system
The functional features of the integrated system are the same as the standard pneumatic system, explained above, with the addition of control through the GreenStar display.
Heavy-duty adjustable downforce springs
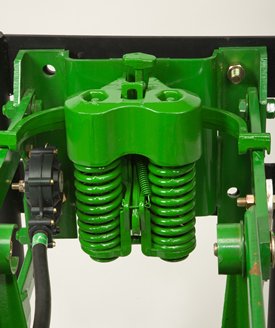
Planter row-unit downforce is an important factor to ensure consistent and proper depth control. The heavy-duty adjustable downforce feature provides up to 181.4 kg (400 lb) of downforce. There are four settings available to allow the operator to choose the amount of downforce required for the condition: 0 kg (0 lb), 56.7 kg (125 lb), 113.4 kg (250 lb), and 181.4 kg (400 lb).
Increase job performance when planting and spraying
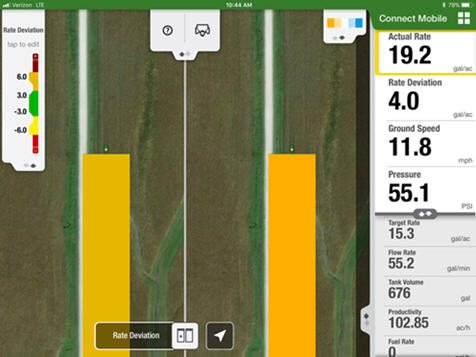
Connect Mobile overview
John Deere Connect Mobile is a solution that utilizes an Apple® iPad® tablet in the cab and helps the operator increase job performance during planting and spraying operations. Connect Mobile documents and displays multiple quality layers, helping the operator monitor and more easily detect problems that can occur during planting and spraying. Connect Mobile also has a common user interface that makes it easy to use between different pieces of John Deere equipment.
Planting attributes
Monitor and document key performance indicators in high-definition map layers and dashboard tiles such as:
- Actual population
- Target population
- Singulation
- Seed-spacing CV
- Applied downforce
- Gauge wheel margin
- Ride quality
- Ground speed
- Variety
Spraying attributes
- Actual rate
- Rate deviation
- Ground speed
- Pressure
In base equipment
Planting
Connect Mobile hardware is factory installed on all model year 2015 and newer planters factory installed with ExactEmerge™ row-units and all model year 2017 and newer planters factory installed with MaxEmerge™ 5e row-units, making it easy to get started with Connect Mobile.
Spraying
Connect Mobile hardware is factory installed on all model year 2018 Sprayers with the 4600 CommandCenter™ display. Producers can also retrofit Connect Mobile on older sprayers with a GreenStar™ 3 2630 Display by installing the sprayer field kit.
Learn more about Connect Mobile in the Field and Crop Solutions section within the Precision Ag Technology product line and how it can improve the quality of a planting and spraying job.
iPad and Apple are trademarks of Apple Inc.
Mobile row-unit runoff
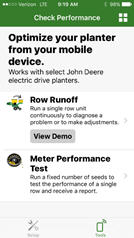
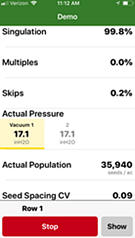
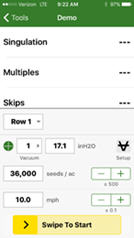
The first day of planting season can be as productive as the last with mobile row-unit runoff. The mobile row-unit runoff activation on the planter main controller (PMC) allows operators to make adjustments to maximize row-unit performance from a mobile device at the rear of the planter for both preseason and in-season use - all enabled through the PlanterPlus™ app.
Mobile row-unit runoff allows growers to perform test-stand functions from a mobile device connected to the planter.
The row runoff test provides complete diagnostic checks both preseason and in season. With the row-unit runoff test, the operator can make adjustments from the mobile device, including vacuum pressure, to determine the optimum meter and vacuum settings. This app functionality will help avoid making trips to the cab while validating meter performance.
During preseason planter inspections and set up, utilize the meter performance test to validate meter accuracy, similar to a test stand without leaving the farm. Test all systems on the planter, not just the meter, providing confidence that all planter systems are ready to plant. Reports are generated from the test providing information the operator can save and send for future reference.
Before heading to the field, the operator will benefit from knowing the best row-unit and vacuum settings for each variety selected to plant that spring.
Watch this video to see mobile row-unit runoff in action.
Mobile row-unit runoff will work with any model year 2015 or newer ExactEmerge™ or MaxEmerge™ 5e equipped planter. Mobile row-unit runoff can be added with attachment AA93169.
For model year 2018 and newer ExactEmerge planters, mobile row-unit runoff is included in base equipment. For model year 2020 and newer MaxEmerge 5e planters, mobile row-unit runoff is included in base equipment. For planters not equipped from the factory, mobile row-unit runoff can be added with attachment AA93169. A mobile row-unit runoff and Easy Fold package can be added with attachment AA97849 (only available with 1775NT and 1795 Planters with a 2-point hitch and model year 2019 and newer DB Planters with Gen 4 based frame folding).
NOTE: Mobile runoff utilizes PlanterPlus app available on select iPad® tablets, iPhone® smartphones, and Android™ devices.
Mobile row-unit runoff and Easy Fold aftermarket for field conversion kits
The below software bundles include the functionality explained above for machines not ordered with the feature from the factory. Compatible machines include all the necessary sensors and harnesses needed to make the feature function. The attachment part is software only. Follow the mobile runoff ordering and software push guide below for ordering and installation.
SeedStar™ 3 HP conversion to SeedStar 4HP
Mobile runoff ordering and software push guide
iPad and iPhone are trademarks of Apple Inc. Android is a trademark of Google LLC.
John Deere Connected Support™ prevents downtime and efficiently resolves issues with revolutionary technology-based solutions
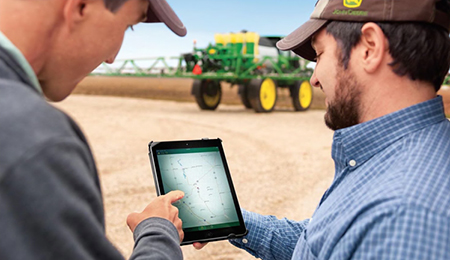
When you buy John Deere equipment, you expect reliability. You also know that problems can happen, and a product is only as good as the support behind it. That’s why John Deere equipment is prepared with technology that senses potential issues and can alert you and your dealer promptly—in the cab or anywhere you are.
John Deere Connected Support is a revolutionary change to support that leverages technology and the connectivity of JDLink™ telematics to prevent downtime and resolve problems faster. These tools decrease downtime by an average of 20 percent, enabling faster responses to unexpected problems and reducing technician trips to your machine. For some issues, unplanned downtime can even be prevented altogether through prediction of the issue.
With your permission, John Deere Connected Support:
- Keeps you running by monitoring machine health and promptly alerting you and your dealer of issues
- Saves time by remotely viewing in-cab displays, reducing trips to the machine
- Reduces or even eliminates technician trips to a machine through remote diagnostic and remote software reprogramming capabilities
- Connects experts with the information needed to respond to downtime faster and prevent it altogether
With more than a decade of experience leveraging connectivity to solve problems, no one else has the experience, tools, and knowledge to keep you running as John Deere and your John Deere dealer can. Connected Support is an in-base feature on all John Deere products with factory- or field-installed JDLink.
Pneumatic closing wheels
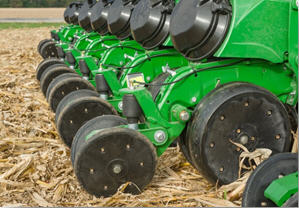
Pneumatic closing wheels are compatible with MaxEmerge™ 5e and ExactEmerge™ row-units. They are available on the following models from the factory: 1775NT, 1795, and DB60 models. The pneumatic closing wheels give operators the ability to adjust closing wheels in seconds without leaving the cab of the tractor.
Using the GreenStar™ 3 2630 Display, pneumatic closing wheels can be adjusted to 25 different positions. From the factory the system is setup with two sections, the outer wings and center frame. With this system, producers will see up to a 76 percent increase in consistent force applied at the closing wheel. Consistently applying the correct force at the seed trench is one of the key elements of supporting improved emergence. Studies show potential yield impact on corn from even emergence from 5 percent to 9 percent*.
NOTE: Pneumatic closing wheels can be purchased for existing MaxEmerge 5e and ExactEmerge planters as an aftermarket field kit. Both rubber tire and cast-iron closing wheels are compatible.
Refer to the operator’s manual for guidance on settings, including when upgrading from springs to pneumatic.
Access the pneumatic closing wheels attachment for field conversion (AFC) ordering guide to fit a 1725 CCS, 1775NT, 1795, or DB60 Planter.
*Source: Planting Outcome Effects on Corn Yield: Doerge, Tom, Jeschke, Mark and Carter, Paul