John Deere 994 Rotary Platform
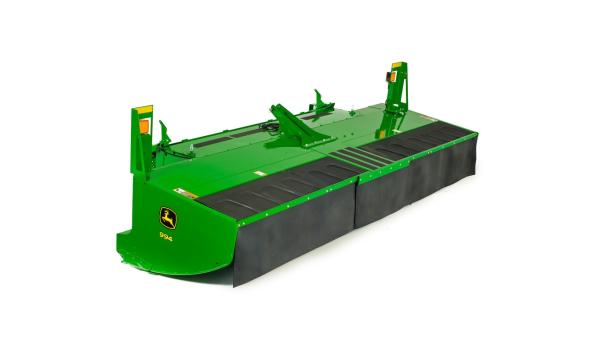
Description
- Rotary cutterbar components
- Patented diagonally cut module
- Hydraulic cutterbar angle adjustment
- Adjustable impeller conditioning hood
Models
Windrow formation
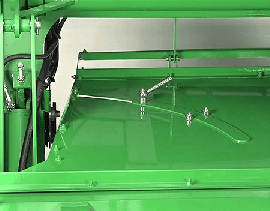
Forming shields are easily adjusted to control the material flow. This allows the operator to match the windrow width to the harvesting requirements.
The adjustable swathboard controls the angle at which the crop flow contacts the forming shield providing additional control of windrow formation.
The windrow width is adjustable, without the use of tools, from a narrow windrow to a wide, fast-drying swath:
- 91.4 cm (36 in.) up to 216 cm (85 in.) with the roll conditioner
- 114.3 cm (45 in.) up to 216 cm (85 in.) with the impeller conditioner
NOTE: The windrow width depends on the crop conditions and type of conditioner.
Designed for use with W200 Series Self-Propelled Windrower
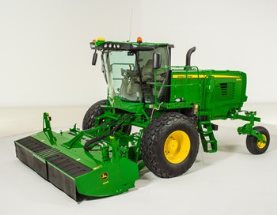
The 994 Rotary Platforms are designed for use with the W200 Series Self-Propelled Windrowers.
The 4-m (13-ft) and 4.5-m (14-ft, 6-in.) cutting widths meet the requirements of large hay growers and commercial operators who want to get the job done fast.
The rotary platform design cuts crop faster in thick, tall, wet, heavy hay or in fields with gopher mounds.
Conditioner choices
Impeller conditioner
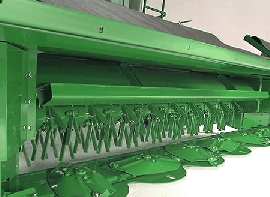
Exclusive impeller conditioner is available for the 994 Rotary Platform. Proper conditioning in a wide range of crops can be achieved when the conditioner is properly adjusted.
How an impeller conditioner works:
1. As hay is cut by rotating knives, 72 V-shaped tines pick up plants and carry them through the machine. The free-swinging design reduces damage to the conditioner if rocks or other solid objects are struck.
- Tines are evenly spaced along the full width of the rotor
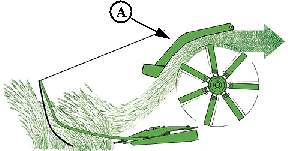
2. As the plant passes through, it rubs against the conditioning hood (A) and other plants. A rubbing action removes the waxy surface from the stem of the plant to allow faster evaporation of moisture.
3. The conditioner hood is adjustable to control the conditioning intensity. The wider the opening, the less aggressive the conditioning; this is used in legume-type crops. The smaller the opening, the more aggressive the conditioning; this is used more in grass hay.
4. The impeller has two speeds to match crop conditioning requirements:
- Simply interchange the drive sheaves
- High speed of 865 rpm for grass hay
- Low speed of 624 rpm for legumes
The impeller conditioner works well in legumes, especially alfalfa and most all-grass crops. Impeller conditioners are not recommended for thick-stemmed or cane-type crops over 1.5-m (5-ft) tall.
Urethane conditioning rolls
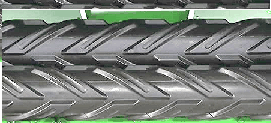
The urethane roll conditioner works well in legumes, especially alfalfa and most all-grass crops. In general, roll conditioners are better suited for thick-stemmed, cane-type, and taller grasses over 1.5-m (5-ft) tall.
Molded urethane rolls are formed by a cool molding process that does not distort or warp the steel core of the roll and ensures the rolls are arrow straight and cylindrical, so they can be accurately spaced close together for uniform conditioning along the length of the roll.
The intermittent recessed cleat design gives more crimping edges for greater pressure per square inch, which results in superior conditioning and faster crop drying.
V-10 steel conditioning rolls
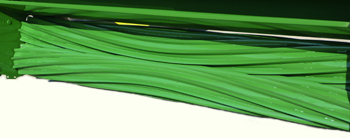
The V-10 steel conditioner rolls feature 10 angled flutes arranged in a chevron, or V, pattern along the length of the steel core.
The steel rolls offer improved wear life over urethane rolls, particularly in adverse crop conditions.
Advantages of the V-10 conditioner roll over the previous straight flute design include the following:
- Deep intermeshing angles for positive feeding and uniform conditioning throughout the entire length of the rolls
- More crimping edges for improved conditioning
- Improved feeding
- Improved windrow formation
Tri-Lobe™ steel conditioning rolls
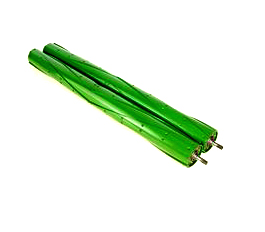
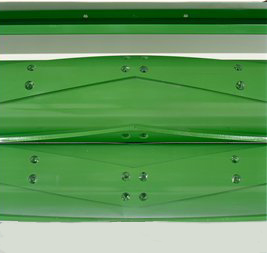
Tri-lobe steel conditioning rolls have three intermeshing chevron lobes to crush the length of the stem for improved conditioning and faster drydown. The rolls are manufactured using a patented process.
The steel material increases wear life, especially in abrasive crops or soil conditions. Durability is a distinct advantage compared to other crusher-style rolls made of rubber or urethane. The chevron design of the rolls gives positive feeding and improved crop flow.
These rolls are well suited for use in alfalfa, where a reduced curing time results in less bleaching of the crop. In heavy, thick-stemmed crops, such as sudan or sudex, the steel construction of the rolls does a very good job of breaking up the nodes on the stems to improve drydown.
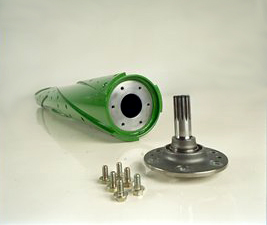
The shafts on the Tri-Lobe rolls are steel forgings that are then machined. These precision parts have minimal run-out, which means the rolls themselves rotate precisely around their axis.
This precision enables the rolls to be adjusted to a minimum clearance for consistent conditioning along the length of the rolls.
The machined, forged roll ends are bolted into the core of the Tri-Lobe steel roll. In the event a roll end were to be damaged, the entire roll does not need to be replaced. Each shaft can be replaced individually, resulting in lower repair costs.
For serviceability, each roll end has two threaded holes so bolts can be used to pull the shafts from the steel core of the roll.
Modular-design cutterbar
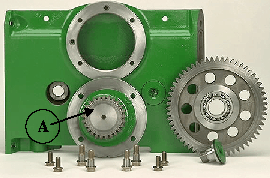
The John Deere-patented-design cutterbar is made from individual, diagonal-cut modules.
Serviceability is easy. Modules can be removed individually while leaving the cutterbar attached to the frame.
The modules are made of high-strength nodular iron castings. Each module consists of two idler gears and one drive gear. The large-diameter idler gears transmit power from module to module. The idler gears turn at a relatively slow speed for added durability.
A smaller-diameter pinion drive gear is used only to power the cutting disk. Power is not transmitted from one cutting disk to another except through the large-diameter idler gears.
Modules are interchangeable. Disc rotation is determined by the position of the quill (A).
There is a rubber oil seal between each cutting module.
Rotary cutterbar components

Large oval discs with free-swinging knives are used to cut the crop.
Knives are free-swinging to reduce damage if solid object is struck.
-
Knife tip speed is variable and can be adjusted from the cab to improve cutting in light crop conditions
-
Knives are reversible to double useful life
-
Knives are removed and replaced at the front of cutterbar for convenience
- All cutting discs are the same size
- Disks are computer-designed for improved wear and cutting performance
- Cutting discs are made of high-strength austempered steel
-
Austemper heat-treating process assures that the steel is thoroughly and evenly tempered for good wear characteristics
-
Wear caps
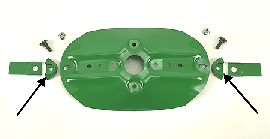
Wear caps are installed on each end of the cutting discs (except on the end disks where crop accelerators are used) to increase the wear life of the cutting discs and knife bolt nuts.
Wear caps are open on the end to prevent debris from packing in close to the nut, making hardware and knives easier to change.
Made of austempered heat-treated ductile steel.
Specifications
- Dimensions - Cutting height: 1.7-17.8 cm<br/>0.7-7 in.
- Dimensions - Cutting width: On 4 m (13 ft): 3.9 m<br/>13 ft<br/>On 4.4 m (14.5 ft): 4.4 m<br/>14.5 ft
- Dimensions - Overall width (transport): On 4 m (13 ft): 4 m<br/>13.1 ft<br/>On 4.4 m (14.5 ft): 4.5 m<br/>14.6 ft
- Dimensions - Weight: With impeller conditioner<br/>On 4 m (13 ft): 1,624 kg<br/>3,565 lb<br/>On 4.4 m (14.5 ft): 1,724 kg<br/>3,800 lbWith fluted steel conditioner<br/>On 4 m (13 ft): 1,696 kg<br/>3,739 lb<br/>On 4.4 m (14.5 ft): 1,848 kg<br/>4,074 lbWith urethane conditioner<br/>On 4 m (13 ft): 1,700 kg<br/>3,749 lb<br/>On 4.4 m (14.5 ft): 1,807 kg<br/>3,984 lbWith Tri-Lobe conditioner<br/>On 4 m (13 ft): 1,864 kg<br/>4,110 lb<br/>On 4.4 m (14.5 ft): 1,970 kg<br/>4,345 lb
- Dimensions - Windrower width (depending on crop conditions): With roll conditioner<br/>91.4-215.9 cm<br/>36-85 in.With impeller conditioner<br/>114.3-215.9 cm<br/>45-85 in.
- Impeller conditioner - Conditioner hood: Adjustable, one lever
- Impeller conditioner - Diameter: 59 cm<br/>23.4 in.
- Impeller conditioner - Drive: 4-V powerband belt and sheaves
- Impeller conditioner - No. of speeds: Factory setting: 624 or 865 rpm<br/>Optional 1,000 rpm
- Impeller conditioner - No. of V-tines: 72
- Impeller conditioner - Width: 2.7 m<br/>8.8 ft
- Rotary disk cutterbar - Guard angle: Adjustable; 0-8 degree (angle)
- Rotary disk cutterbar - Number of disks: 8 on 13-ft; 9 on 14.5-ft.
- Rotary disk cutterbar - Reservoir capacity: On 4 m (13 ft): 9.5 L<br/>10 U.S. qt<br/>On 4.4 m (14.5 ft): 10.4 L<br/>11 U.S. qt
- Steel conditioner rolls - Diameter: 25.4 cm<br/>10 in.
- Steel conditioner rolls - Drive: Enclosed gear and shaft drive
- Steel conditioner rolls - Material: Steel
- Steel conditioner rolls - Speed: 865 rpm
- Steel conditioner rolls - Surface: Intermeshing flutes
- Steel conditioner rolls - Width: 2.7 m<br/>8.8 ft
- Urethane conditioner rolls - Diameter: 25.4 cm<br/>10 in.
- Urethane conditioner rolls - Drive: Enclosed gear and shaft drive
- Urethane conditioner rolls - Material: Urethane
- Urethane conditioner rolls - Speed: 64 rpm
- Urethane conditioner rolls - Surface: Intermeshing flutes
- Urethane conditioner rolls - Width: 2.7 m<br/>8.8 ft
- Windrower - Compatibility: 4995, R450, W235, W260
- Windrower - Formation: Adjustable swath board and adjustable forming shields
Copy Set
Windrow formation
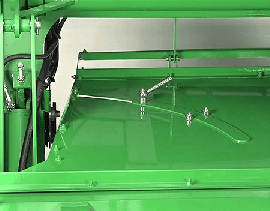
Forming shields are easily adjusted to control the material flow. This allows the operator to match the windrow width to the harvesting requirements.
The adjustable swathboard controls the angle at which the crop flow contacts the forming shield providing additional control of windrow formation.
The windrow width is adjustable, without the use of tools, from a narrow windrow to a wide, fast-drying swath:
- 91.4 cm (36 in.) up to 216 cm (85 in.) with the roll conditioner
- 114.3 cm (45 in.) up to 216 cm (85 in.) with the impeller conditioner
NOTE: The windrow width depends on the crop conditions and type of conditioner.
Designed for use with W200 Series Self-Propelled Windrower
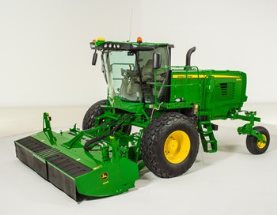
The 994 Rotary Platforms are designed for use with the W200 Series Self-Propelled Windrowers.
The 4-m (13-ft) and 4.5-m (14-ft, 6-in.) cutting widths meet the requirements of large hay growers and commercial operators who want to get the job done fast.
The rotary platform design cuts crop faster in thick, tall, wet, heavy hay or in fields with gopher mounds.
Conditioner choices
Impeller conditioner
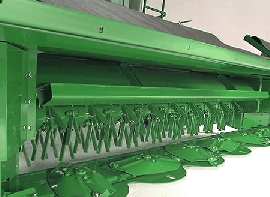
Exclusive impeller conditioner is available for the 994 Rotary Platform. Proper conditioning in a wide range of crops can be achieved when the conditioner is properly adjusted.
How an impeller conditioner works:
1. As hay is cut by rotating knives, 72 V-shaped tines pick up plants and carry them through the machine. The free-swinging design reduces damage to the conditioner if rocks or other solid objects are struck.
- Tines are evenly spaced along the full width of the rotor
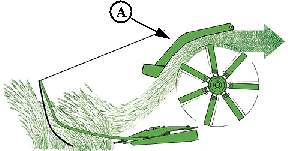
2. As the plant passes through, it rubs against the conditioning hood (A) and other plants. A rubbing action removes the waxy surface from the stem of the plant to allow faster evaporation of moisture.
3. The conditioner hood is adjustable to control the conditioning intensity. The wider the opening, the less aggressive the conditioning; this is used in legume-type crops. The smaller the opening, the more aggressive the conditioning; this is used more in grass hay.
4. The impeller has two speeds to match crop conditioning requirements:
- Simply interchange the drive sheaves
- High speed of 865 rpm for grass hay
- Low speed of 624 rpm for legumes
The impeller conditioner works well in legumes, especially alfalfa and most all-grass crops. Impeller conditioners are not recommended for thick-stemmed or cane-type crops over 1.5-m (5-ft) tall.
Urethane conditioning rolls
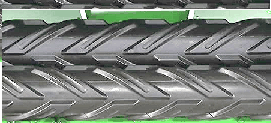
The urethane roll conditioner works well in legumes, especially alfalfa and most all-grass crops. In general, roll conditioners are better suited for thick-stemmed, cane-type, and taller grasses over 1.5-m (5-ft) tall.
Molded urethane rolls are formed by a cool molding process that does not distort or warp the steel core of the roll and ensures the rolls are arrow straight and cylindrical, so they can be accurately spaced close together for uniform conditioning along the length of the roll.
The intermittent recessed cleat design gives more crimping edges for greater pressure per square inch, which results in superior conditioning and faster crop drying.
V-10 steel conditioning rolls
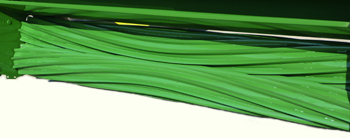
The V-10 steel conditioner rolls feature 10 angled flutes arranged in a chevron, or V, pattern along the length of the steel core.
The steel rolls offer improved wear life over urethane rolls, particularly in adverse crop conditions.
Advantages of the V-10 conditioner roll over the previous straight flute design include the following:
- Deep intermeshing angles for positive feeding and uniform conditioning throughout the entire length of the rolls
- More crimping edges for improved conditioning
- Improved feeding
- Improved windrow formation
Tri-Lobe™ steel conditioning rolls
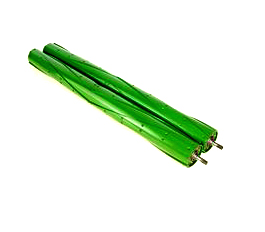
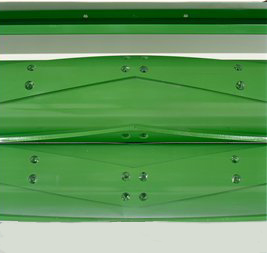
Tri-lobe steel conditioning rolls have three intermeshing chevron lobes to crush the length of the stem for improved conditioning and faster drydown. The rolls are manufactured using a patented process.
The steel material increases wear life, especially in abrasive crops or soil conditions. Durability is a distinct advantage compared to other crusher-style rolls made of rubber or urethane. The chevron design of the rolls gives positive feeding and improved crop flow.
These rolls are well suited for use in alfalfa, where a reduced curing time results in less bleaching of the crop. In heavy, thick-stemmed crops, such as sudan or sudex, the steel construction of the rolls does a very good job of breaking up the nodes on the stems to improve drydown.
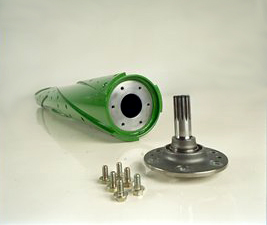
The shafts on the Tri-Lobe rolls are steel forgings that are then machined. These precision parts have minimal run-out, which means the rolls themselves rotate precisely around their axis.
This precision enables the rolls to be adjusted to a minimum clearance for consistent conditioning along the length of the rolls.
The machined, forged roll ends are bolted into the core of the Tri-Lobe steel roll. In the event a roll end were to be damaged, the entire roll does not need to be replaced. Each shaft can be replaced individually, resulting in lower repair costs.
For serviceability, each roll end has two threaded holes so bolts can be used to pull the shafts from the steel core of the roll.
Modular-design cutterbar
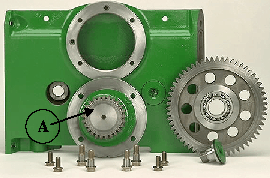
The John Deere-patented-design cutterbar is made from individual, diagonal-cut modules.
Serviceability is easy. Modules can be removed individually while leaving the cutterbar attached to the frame.
The modules are made of high-strength nodular iron castings. Each module consists of two idler gears and one drive gear. The large-diameter idler gears transmit power from module to module. The idler gears turn at a relatively slow speed for added durability.
A smaller-diameter pinion drive gear is used only to power the cutting disk. Power is not transmitted from one cutting disk to another except through the large-diameter idler gears.
Modules are interchangeable. Disc rotation is determined by the position of the quill (A).
There is a rubber oil seal between each cutting module.
Rotary cutterbar components

Large oval discs with free-swinging knives are used to cut the crop.
Knives are free-swinging to reduce damage if solid object is struck.
-
Knife tip speed is variable and can be adjusted from the cab to improve cutting in light crop conditions
-
Knives are reversible to double useful life
-
Knives are removed and replaced at the front of cutterbar for convenience
- All cutting discs are the same size
- Disks are computer-designed for improved wear and cutting performance
- Cutting discs are made of high-strength austempered steel
-
Austemper heat-treating process assures that the steel is thoroughly and evenly tempered for good wear characteristics
-
Wear caps
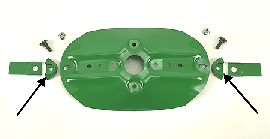
Wear caps are installed on each end of the cutting discs (except on the end disks where crop accelerators are used) to increase the wear life of the cutting discs and knife bolt nuts.
Wear caps are open on the end to prevent debris from packing in close to the nut, making hardware and knives easier to change.
Made of austempered heat-treated ductile steel.